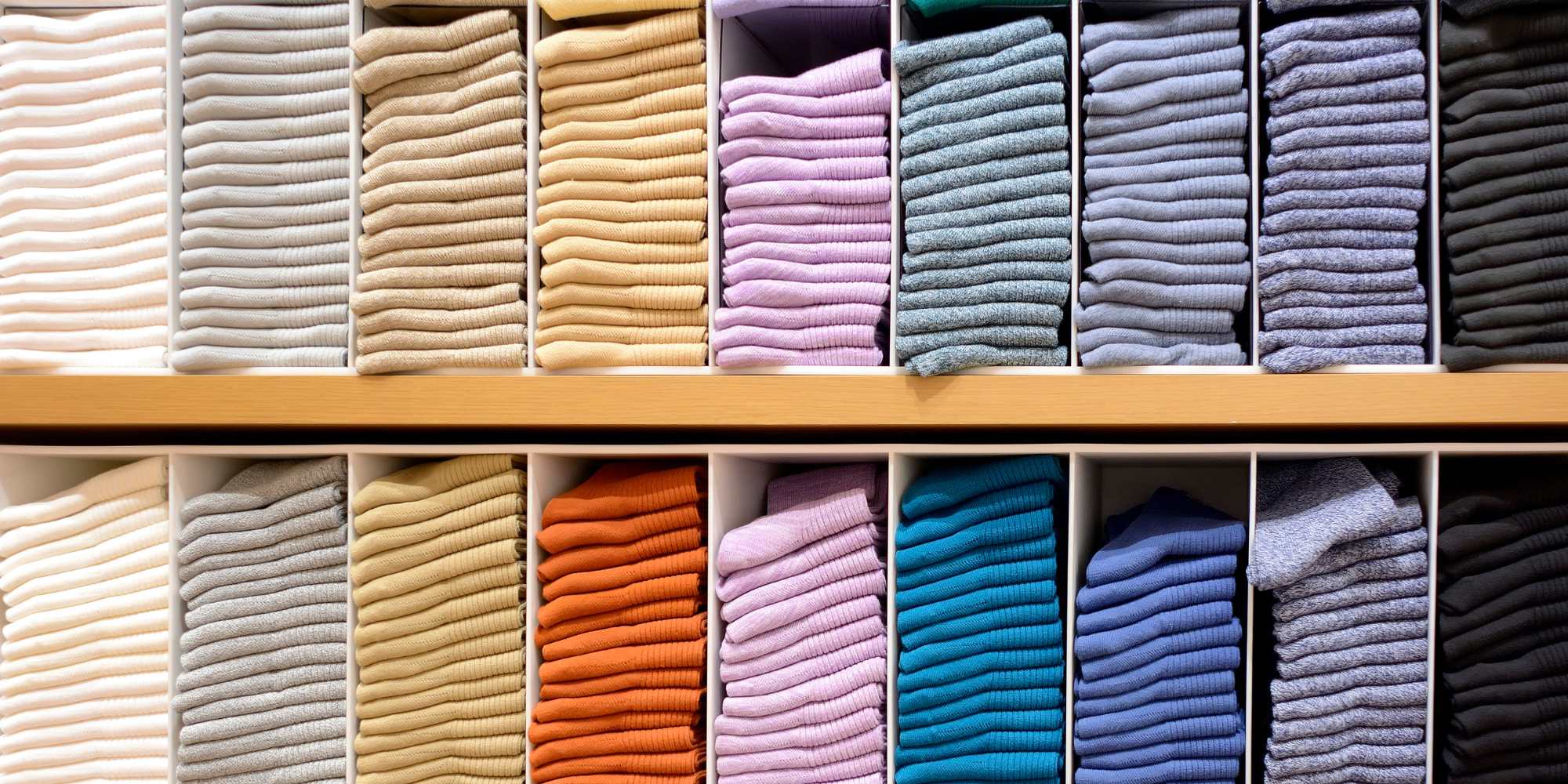
Jump right in: 9 Proven Tips for Quality Control in Apparel Fulfillment
- Introduction
- Tip 1: Vet your suppliers carefully.
- Tip 2: Implement rigorous inspection protocols.
- Tip 3: Establish clear quality standards.
- Tip 4: Train your fulfillment team.
- Tip 5: Leverage technology for quality assurance.
- Tip 6: Implement a returns process.
- Tip 7: Conduct random inspections.
- Tip 8: Set up a way for customers to provide feedback.
- Tip 9: Focus on continuous improvement.
- Summary
Introduction
The apparel industry is a highly competitive world, especially when you are talking about major brands like Coco Chanel, Ralph Lauren, and Clavin Klein! If you are a small brand or just starting, maintaining these types of high standards of quality in your products and partnerships with vendors can make or break your business.
Within the apparel fulfillment process, quality control ensures that every item reaching your end customer base meets the expectations you have set and the promises you have made. Let us jump right in to see what steps you should take to ensure quality control within your fulfillment operations.
Want to learn more about apparel quality control for your brand?
Check out this video by Fit Design TV to get some insights into how to manage the quality control of your apparel production.
Tip #1: Vet your suppliers carefully
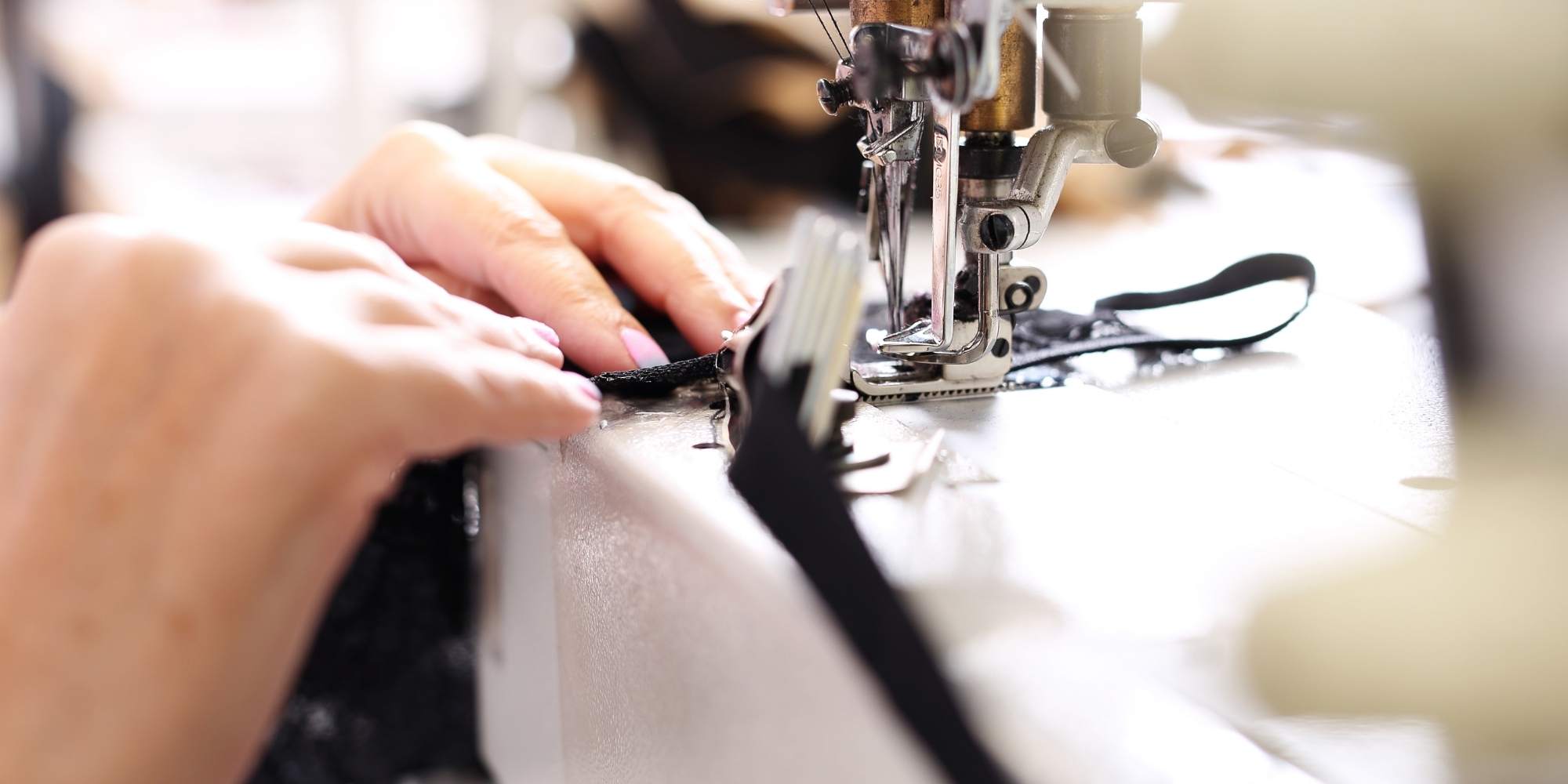
A robust quality control process is essential for ensuring the success and reputation of any business, and it begins long before you choose a Apparel fulfillment provider. The foundation of this process should be in place when choosing the right supplier, as they play a critical role in maintaining the quality of your products. Ensuring that your suppliers align with your quality standards, it is important to conduct thorough research and implement a strict vetting process.
Start by researching potential suppliers extensively, looking into their history, reputation, and customer feedback. Requesting samples of their products is a key step, as it allows you to assess the quality firsthand. If feasible, visiting the supplier’s factories or production facilities can provide valuable insights into their operations, allowing you to observe their production processes, quality control measures, and overall capabilities. This firsthand evaluation can reveal potential issues that might not be evident from a distance.
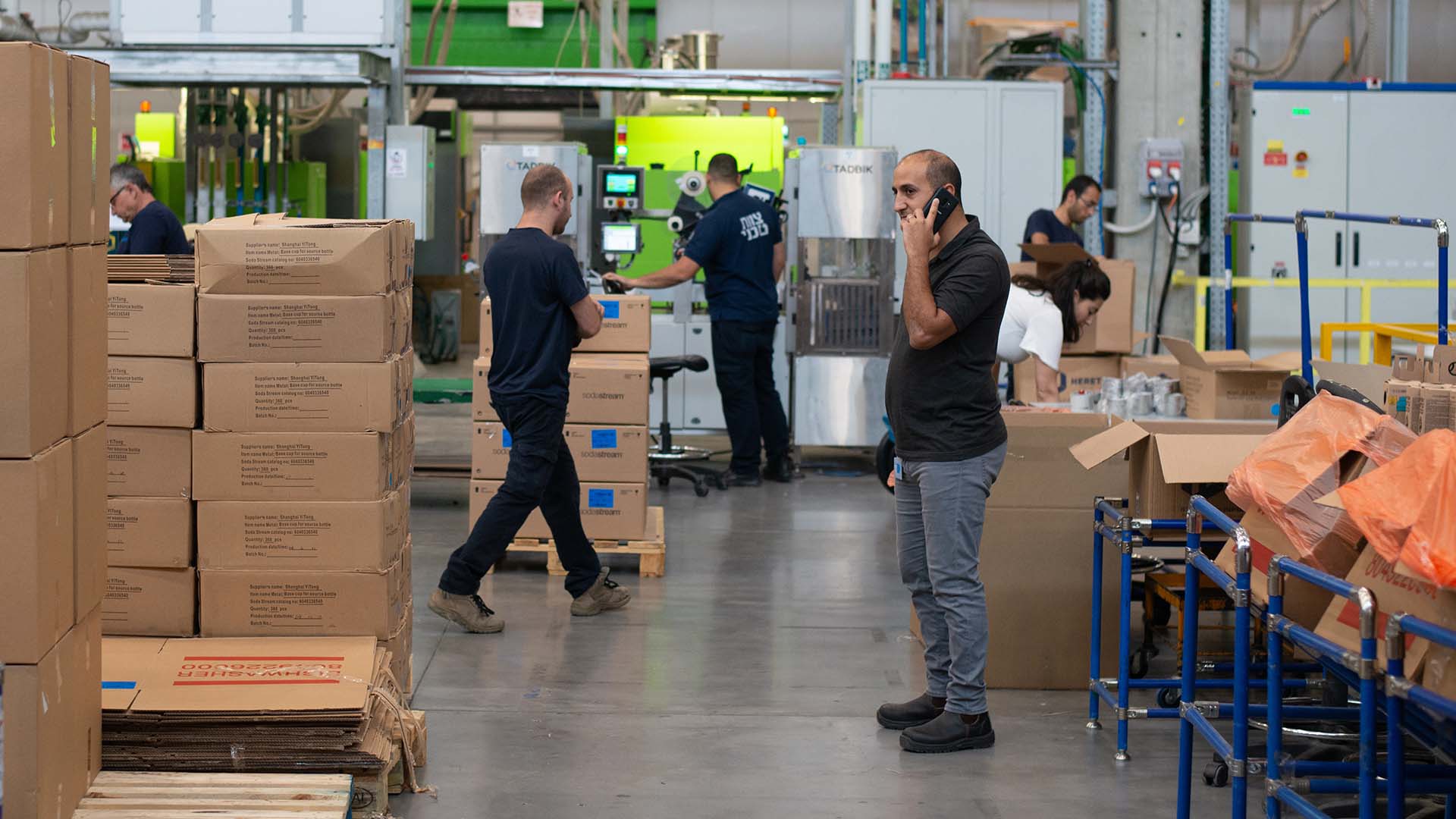
Assessing their production capabilities is another crucial aspect. It is important to ensure that the supplier can meet your production needs, in terms of volume and consistency. This involves evaluating their machinery, workforce, and operational efficiency. A dependable supplier is your first line of defense against quality issues, and establishing a strong, transparent relationship with them is key to maintaining high standards throughout your supply chain. By taking these steps, you can build a solid foundation for your quality control process, significantly reducing the risk of encountering quality issues down the line.
Save Time and Let us Handle Your Apparel Fulfillment!
See How Using a 3PL for saves apparel sellers time. Get a Free Quote from eFulfillment Service Today!
Tip #2: Implement rigorous inspection protocols
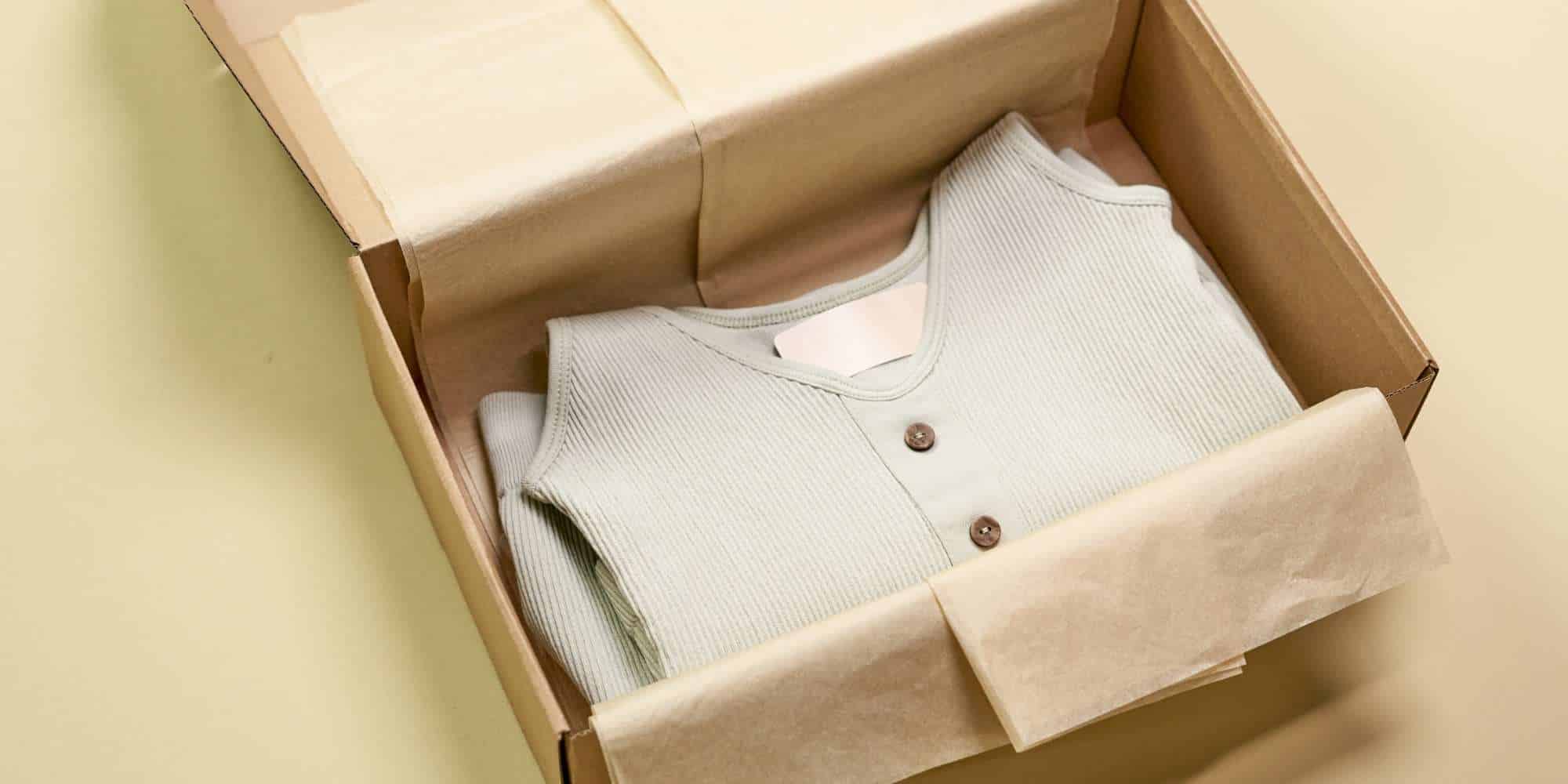
Inspections are a critical component of quality control in the apparel industry. Implement a multi-stage inspection process that includes:
- Pre-production inspection: Ensure all materials and components meet your standards before production begins.
- In-line inspection: By conducting inspections during the production process to catch any issues early. These inspections can still be managed if you are using a facility that is located overseas by requesting samples or having a partner with boots on the ground.
- Final inspection: Perform a detailed inspection of the finished products before they leave the factory or warehouse.
These inspections should be conducted by you or trained professionals that are familiar with your quality standards and expectations.
Tip #3: Establish clear quality standards
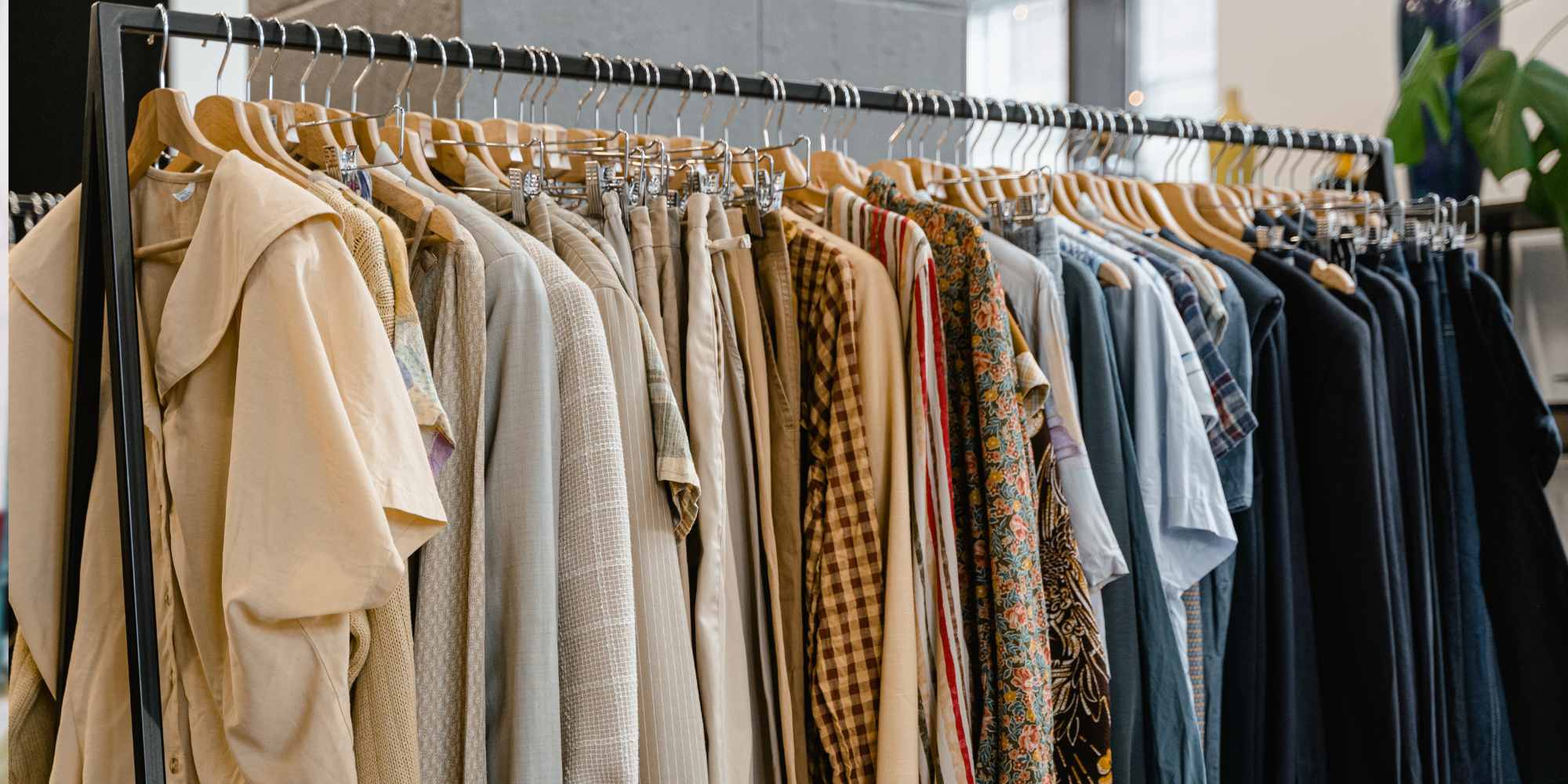
To ensure top-notch quality control for your apparel line, the first step is to establish, and comprehensive quality standards. These standards should be detailed, covering every aspect of your products to maintain consistency and excellence. Start by defining the required fabric quality, specifying the type of material, thread count, and any other relevant characteristics. Additionally, set guidelines for stitching, ensuring that seams are strong, neat, and uniform across all items. Stitch consistency can play a crucial role within your line so knowing the finer details of what enables consistency matters.
Color accuracy is another element, as even slight variations can significantly affect the overall look and feel of your apparel. Size consistency is equally important, with precise measurements and tolerances to guarantee that each item meets the expected fit and dimensions. The overall appearance should be evaluated, with attention to details such as finish, packaging, and presentation.
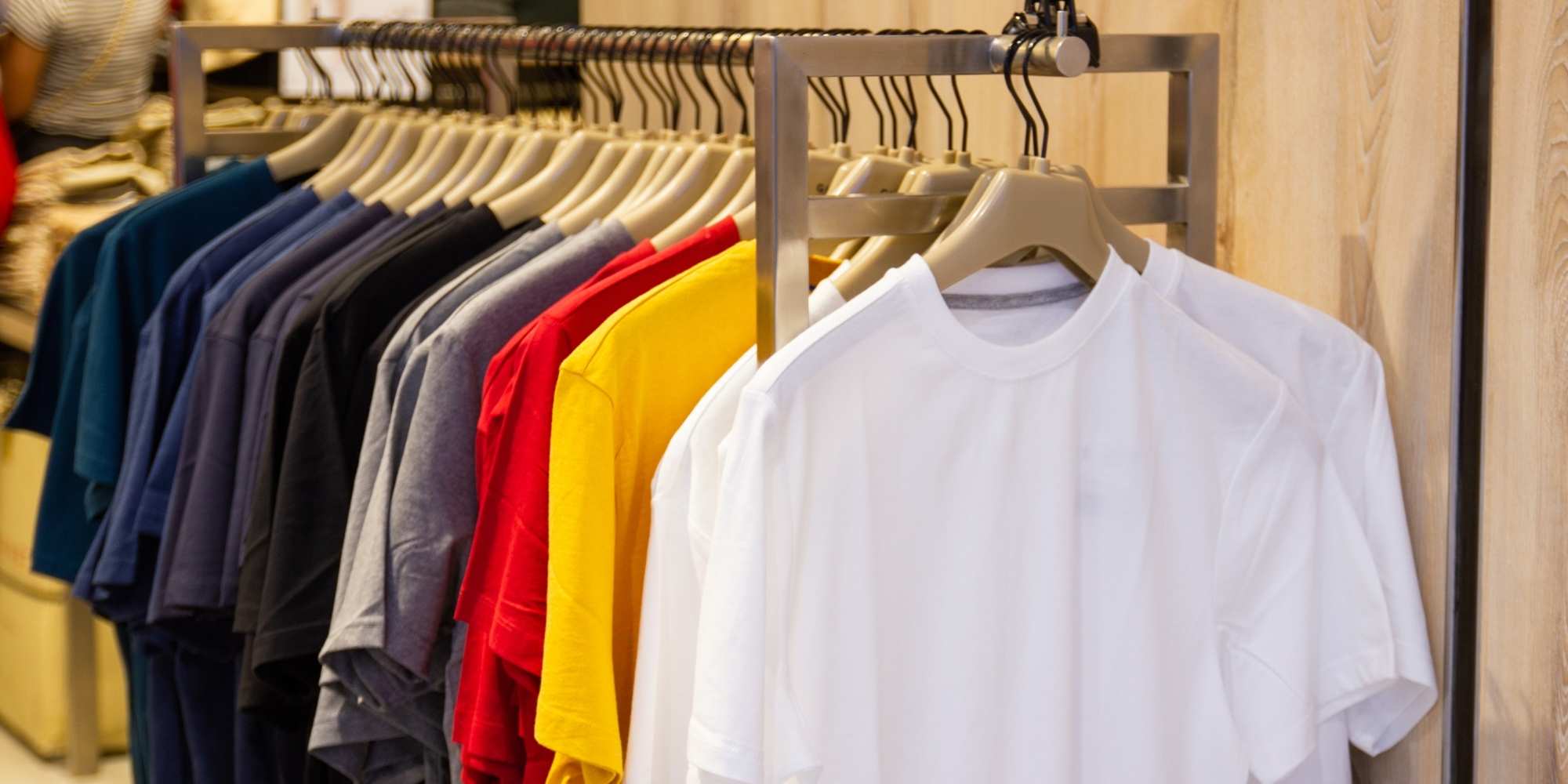
Documenting these quality standards is essential for maintaining consistency and accountability. Once these standards are outlined, it is important to communicate them clearly and effectively to all parties involved in the production process. This includes manufacturers, suppliers, and the quality control team at your fulfillment center.
Tip #4: Train your fulfillment team
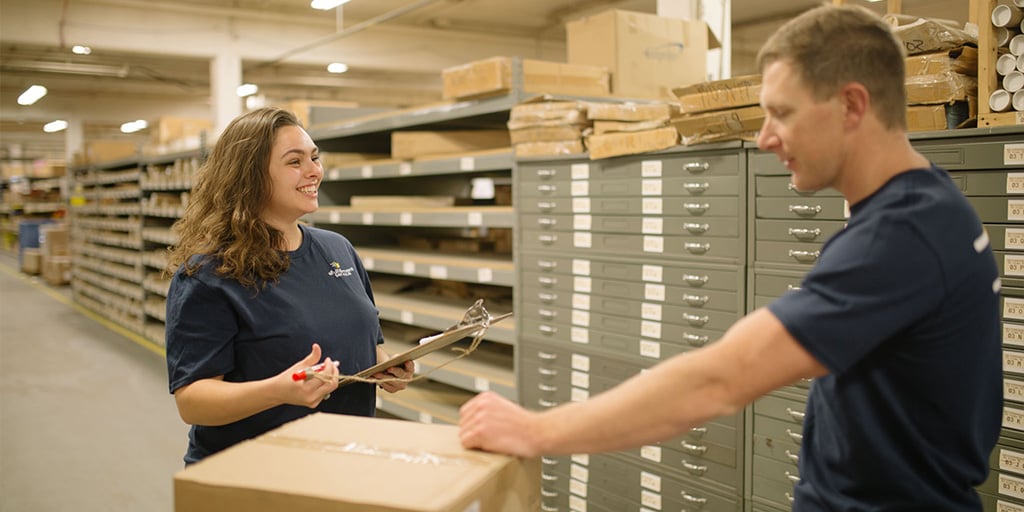
Within any e-commerce business, your fulfillment partner plays a crucial role in ensuring quality. Make sure to outline what your quality standards are at the beginning of your relationship.
This means having clear instructions on what you find is acceptable and when you would like something not shipped. This will empower your fulfillment team to make decisions based on your requirements during the receipt of the inventory, as well as shipping it out the door.
This will ensure that the fulfillment team has the tools needed to live up to your and the end customer’s expectations.
Tip #5: Leverage technology for quality assurance
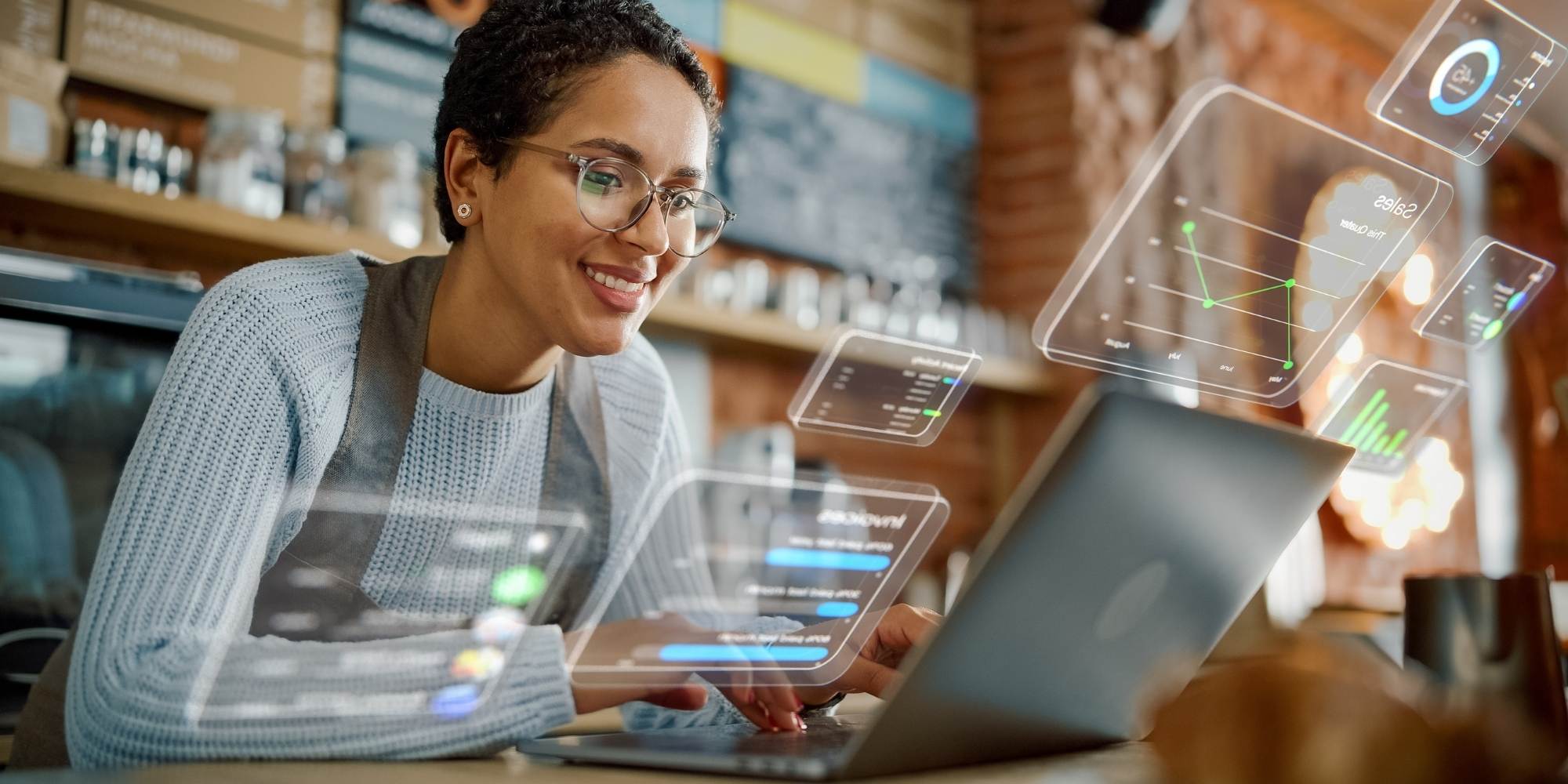
Technology plays a significant role in any e-commerce business but can truly enhance the quality control portion of an apparel line. By utilizing a software solution that allows you to be able to track metrics in real-time, monitor production processes, and quickly identify and address issues will help head off stock outs and keep your customers happy.
When selecting an apparel manufacturer, make sure they use automation software for patterns, and fabric cutting areas to reduce human error and ensure consistency each time they complete a run. This will ensure that your sizing stays true each time.
Tip #6: Implement a hassle-free returns process
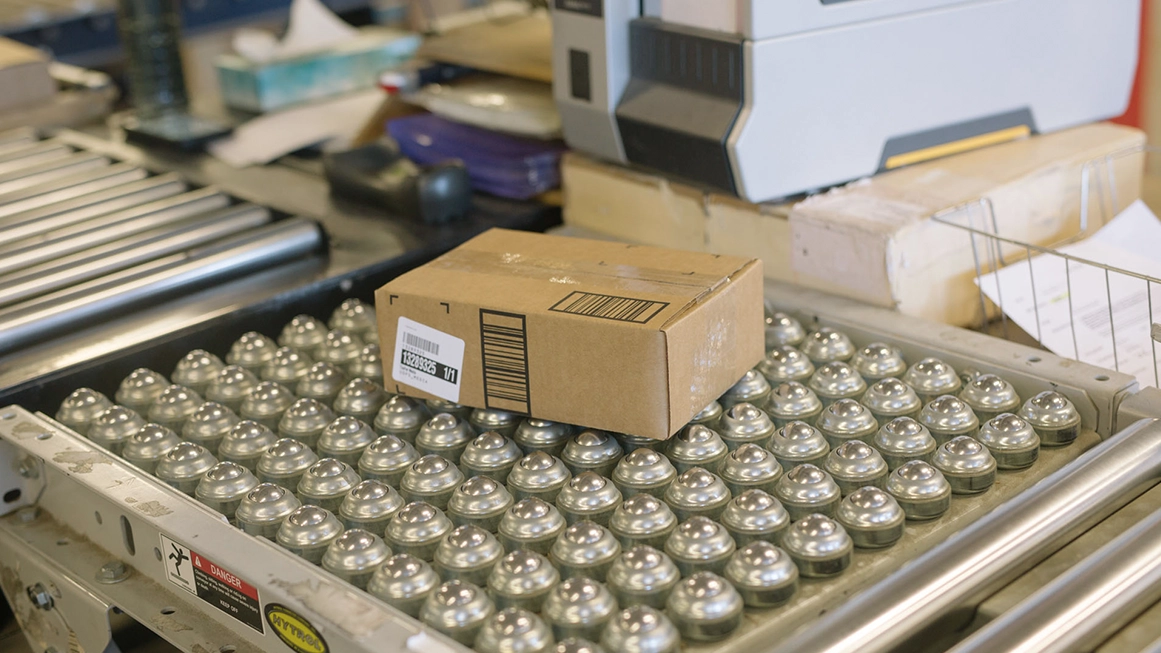
No quality control process would be complete without a system for managing the returns process. Selecting a 3PL warehouse that offers return processing, from creating a return label to receiving and processing the return is key within the apparel industry.
If they also allow you to track the condition of the return during the receipt, this will help you be able to streamline this process for you and your customers, maintaining customer satisfaction.
Apparel Returns Statistics:
- Return Rates: The average return rate for e-commerce is typically between 20% and 30%. Specifically, clothing has a high return rate, with about 26% of items being returned.
- Financial Impact: In 2022, e-commerce returns amounted to approximately $203.22 billion, highlighting the financial significance of managing returns effectively.
- Customer Preferences: A significant 92% of customers are likely to make repeat purchases if the returns process is easy, emphasizing the importance of a streamlined returns management system.
Efficiency Tip: Partnering with an 3PL can free up your time to focus on what you do best, sell great apparel!
Get a Free Quote from eFulfillment Service and see how we can simplify your apparel selling!
Tip #7: Conduct random inspections
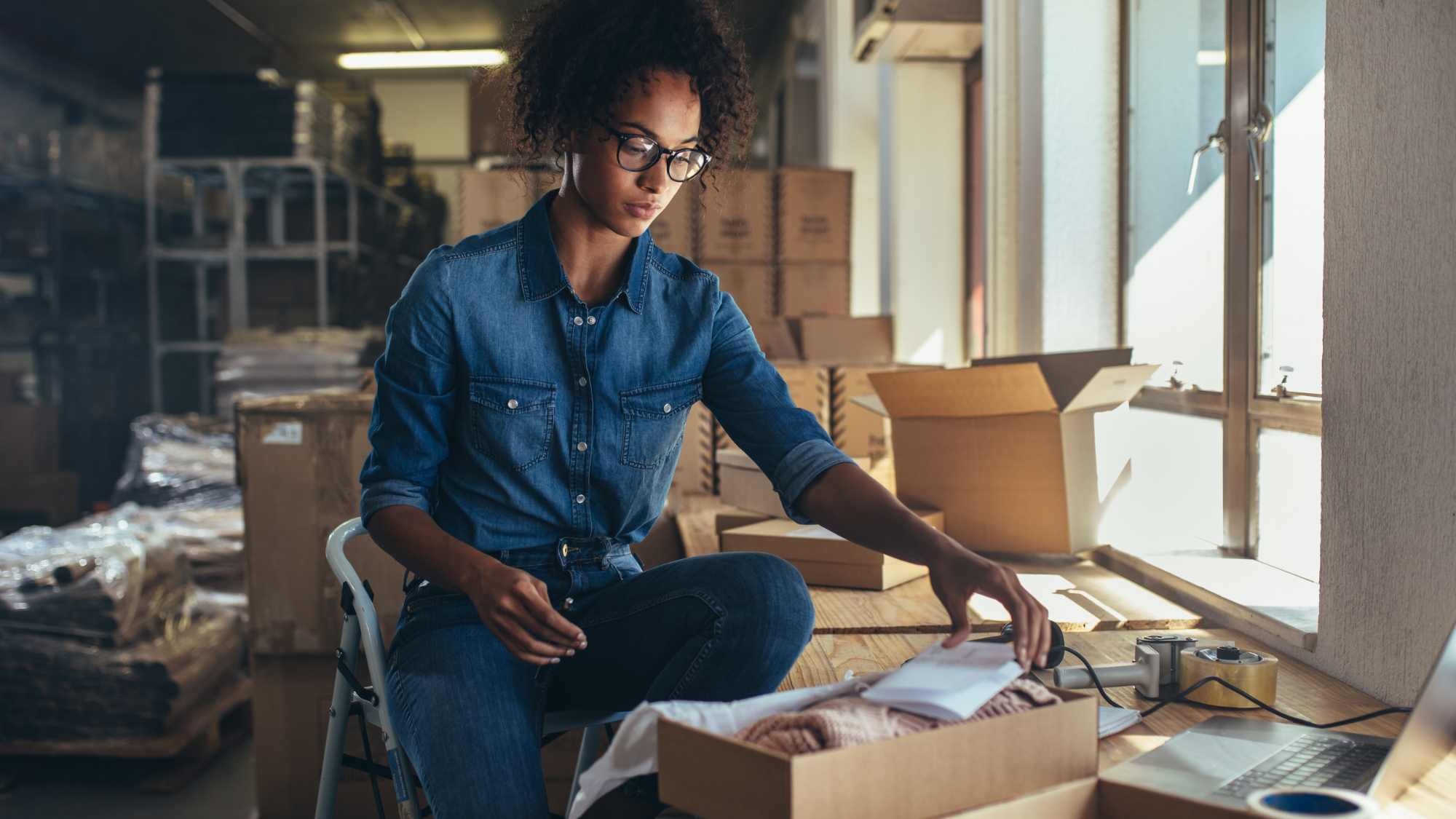
Even with all these processes in place, it is essential to conduct random inspections with your suppliers and fulfillment provider, allowing you to ensure that your quality control processes are being adhered to.
This will also allow you to see firsthand how effective the protocols you set are working and will also allow you to make improvements as needed. Make sure to stay updated on industry trends and best practices, be willing to adapt your strategies to maintain high standards.
Tip #8: Set up a way for customers to provide feedback
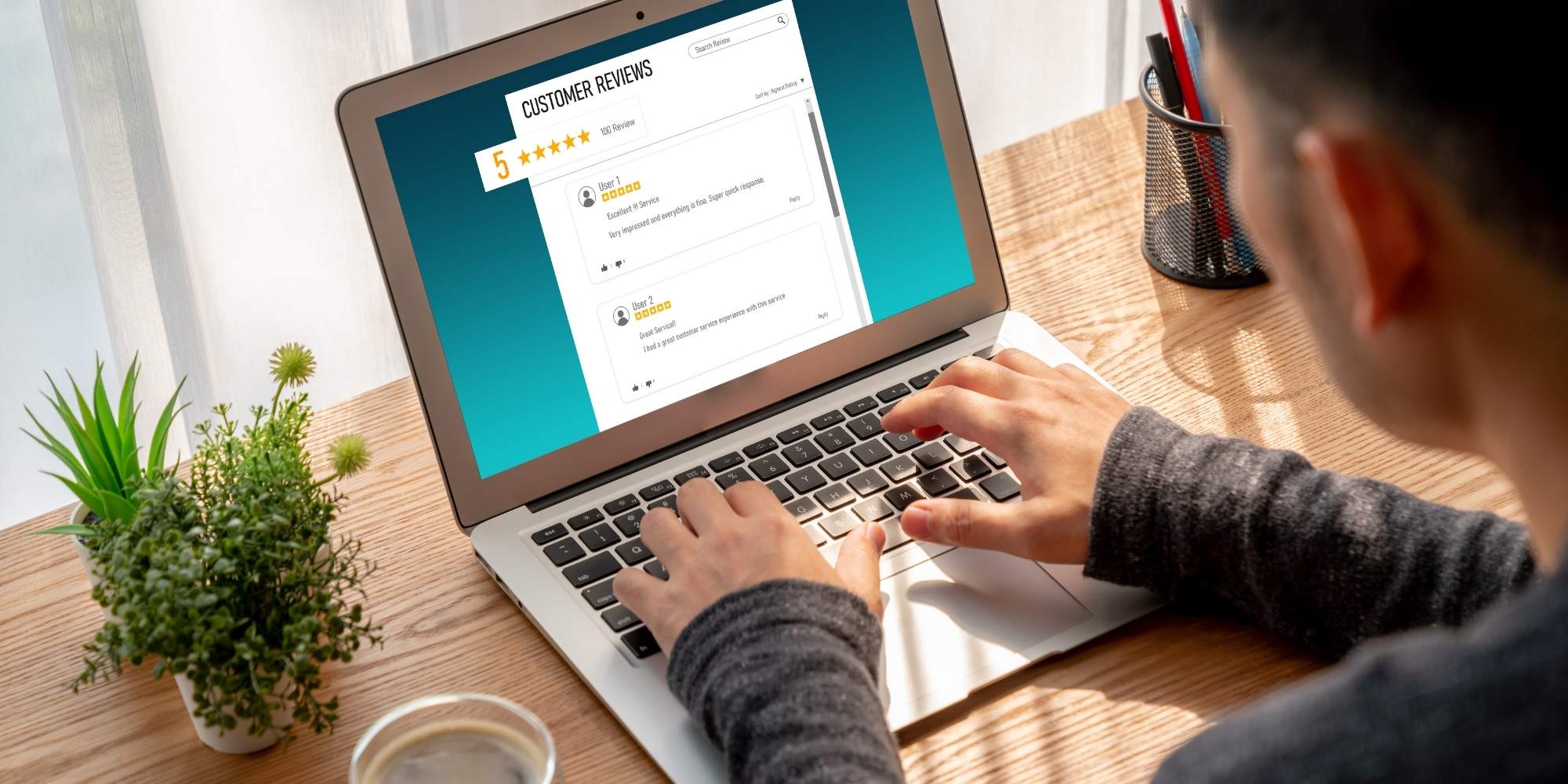
Providing a way for your customers to be able to provide you with feedback will pave the way for ongoing customer retention. There are several avenues that you can use for your customers to contact you.
Make sure your customers can speak with agents directly via phone, email, or instant chat to help resolve any sizing, fabric, or shipping time questions. Sending out satisfaction surveys also allows you to be able to get uncensored feedback not only about your product but also about your customer support. This will let you know areas that need improvement.
Consumer Behavior: Around 30% of all products ordered online are returned, which is significantly higher than the 8.89% return rate in brick-and-mortar stores. This indicates the importance of addressing product dissatisfaction and sizing issues in online sales.
Return Reasons: Common reasons for returns include damaged products (20%), items looking different than expected (22%), receiving the wrong item (23%), and other unspecified reasons (35%).
Tip #9: Focus on Continuous improvement
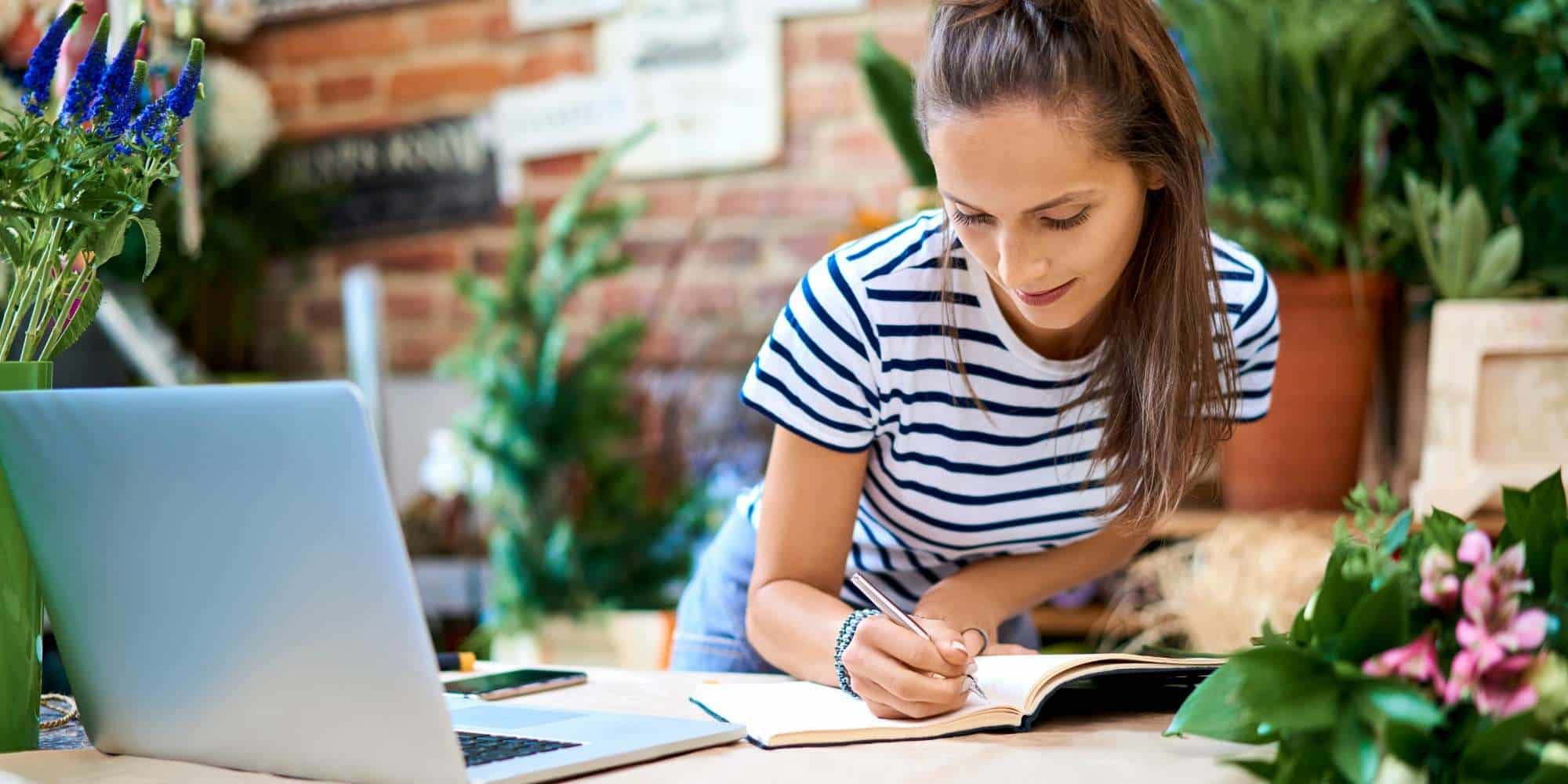
Quality control is not a one-time effort but an ongoing process. Regularly reviewing your quality processes and assessing their effectiveness, will allow you to make improvements as needed.
In today’s market, customers want instant gratification. Staying on top of your suppliers and manufacturers will allow you to be able to prevent stockouts and keep your customers satisfied when they are not needing to wait due to something being out of stock.
Want Fast, Hassle-Free Apparel Fulfillment for Your Brand?
Using a 3PL can free up your time so you can focus on what matters, selling great apparel!
FAQs: Apparel Quality Control
What is quality control in the apparel industry?
Quality control in the apparel industry refers to the systematic process of ensuring that garments and accessories meet predetermined quality standards before they reach the customer. This involves various checks and measures throughout the production and fulfillment processes, including:
- Inspecting raw materials
- Monitoring production processes
- Checking finished products for defects
- Ensuring accurate sizing and color consistency
- Verifying packaging and labeling accuracy
The goal of quality control is to maintain consistent product quality, reduce defects, and ensure customer satisfaction.
What is quality standard in apparel industry?
Quality standards in the apparel industry are predetermined specifications and criteria that garments must meet to be considered acceptable. These standards typically cover various aspects of the product, including:
- Material quality and composition
- Construction and stitching
- Color accuracy and consistency
- Size and fit
- Durability and performance
- Appearance and finish
- Compliance with safety regulations
Quality standards are usually set by the brand or manufacturer based on industry norms, customer expectations, and specific brand requirements.
What is the difference between QA and QC in apparel industry?
While often used interchangeably, Quality Assurance (QA) and Quality Control (QC) have distinct roles in the apparel industry:
- Quality Assurance (QA): • Focuses on preventing defects • Involves planning and systematic activities • Aims to establish processes that ensure quality • Is proactive and process-oriented
- Quality Control (QC): • Focuses on identifying defects • Involves inspection and testing of products • Aims to verify that quality standards are met • Is reactive and product-oriented
In simple terms, QA works to prevent problems, while QC works to identify and solve problems.
What is the QA process in garment industry?
The Quality Assurance (QA) process in the garment industry typically includes the following steps:
- Setting quality standards and specifications
- Developing and implementing quality management systems
- Training staff on quality procedures and best practices
- Establishing process controls and monitoring systems
- Conducting regular audits of production processes
- Analyzing data to identify trends and areas for improvement
- Implementing corrective and preventive actions
- Continuously reviewing and updating quality processes
The QA process aims to create a system that consistently produces high-quality garments by focusing on the entire production cycle rather than just the end product.
What is acceptable quality level in garment industry?
Acceptable Quality Level (AQL) in the garment industry is a statistical tool used to determine the maximum number of defects that can be considered acceptable during random sampling inspections. The AQL is typically expressed as a percentage or ratio of defective items to the total number of items in a lot.
Common AQL levels in the garment industry include:
- 2.5 AQL: Allows 2.5% defectives (often used for general apparel)
- 1.5 AQL: Allows 1.5% defectives (used for more critical items)
- 1.0 AQL: Allows 1.0% defectives (used for high-end or safety-critical items)
The specific AQL used can vary based on:
- Brand requirements
- Product type and complexity
- Target market expectations
- Regulatory standards
It's important to note that while AQL provides a benchmark for acceptance, many brands strive for even higher quality levels to maintain customer satisfaction and brand reputation.
Summary
Ensuring quality control in apparel fulfillment requires a strategic approach, meticulous planning, and unwavering dedication to excellence. By implementing these steps, you can foster customer loyalty, enhance brand credibility, and drive long-term success. Remember, quality control is not just about meeting customer expectations—it’s about exceeding them and setting your brand apart in a competitive marketplace.
Partnering with a seasoned third-party logistics provider (3PL) can further bolster your quality control efforts, ensuring proper packaging and accurate delivery. By prioritizing quality at every stage of your fulfillment operations, you’re investing in your brand’s future and customer satisfaction.
Key Takeaways
- Supplier vetting is crucial: Carefully select and maintain relationships with suppliers who meet your quality standards.
- Multi-stage inspections are essential: Implement pre-production, in-line, and final inspections to catch issues early.
- Clear standards drive consistency: Establish and communicate comprehensive quality standards for all aspects of your products.
- Team training is vital: Empower your fulfillment team with the knowledge to make informed quality decisions.
- Technology enhances quality control: Leverage software and automation to monitor and improve your processes.
- Efficient returns management matters: Choose a 3PL that can handle returns effectively and provide valuable insights.
- Random inspections maintain standards: Regularly perform unannounced quality checks to ensure ongoing compliance.
- Customer feedback is invaluable: Set up multiple channels to gather and act on customer input.
- Continuous improvement is key: Regularly review and update your quality processes to stay competitive.
0 Comments