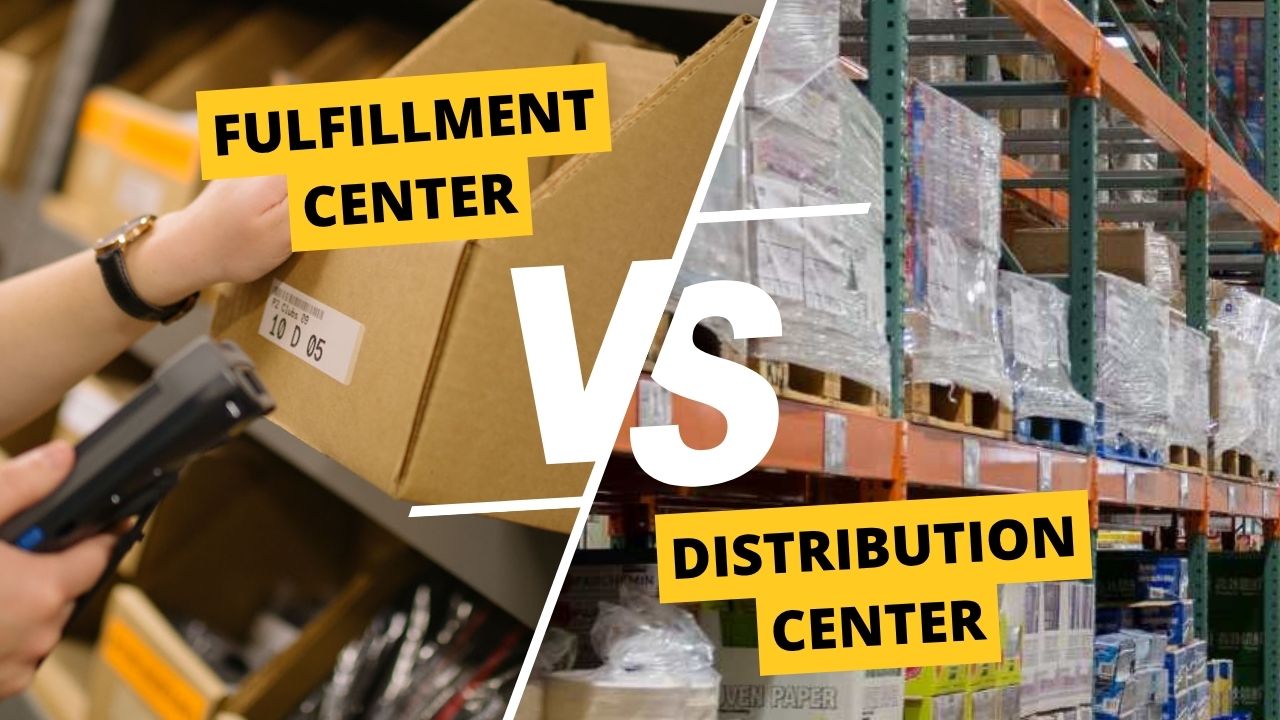
Ever wondered why your online order sometimes ships straight to your door in a neat little box, while other products take a detour through a warehouse network before reaching store shelves? Here’s the thing: it comes down to fulfillment centers vs distribution centers – two terms people often mix up, yet they play very different roles in getting products from point A to point B. If you’re a business owner or ecommerce seller, knowing the difference isn’t just jargon; it can make or break how efficiently you serve your customers. So, let’s clear the air (in a friendly, non-jargony way) on what each does, how they differ, and which one might be right for your business.
Jump right in: Fulfillment Center vs Distribution Center: Understanding the Differences
What Is a Fulfillment Center?
A fulfillment center is essentially a bustling hub dedicated to processing and shipping individual customer orders. Think of it as the last stop for a product before it lands on a customer’s doorstep. These centers store inventory for ecommerce merchants and handle all the steps of order fulfillment – receiving products, picking the items when orders come in, packing them up, and shipping them out via parcel carriers. In other words, when you click “Buy Now” on a website, a fulfillment center is where the magic happens to get that item in a box and on its way to you.
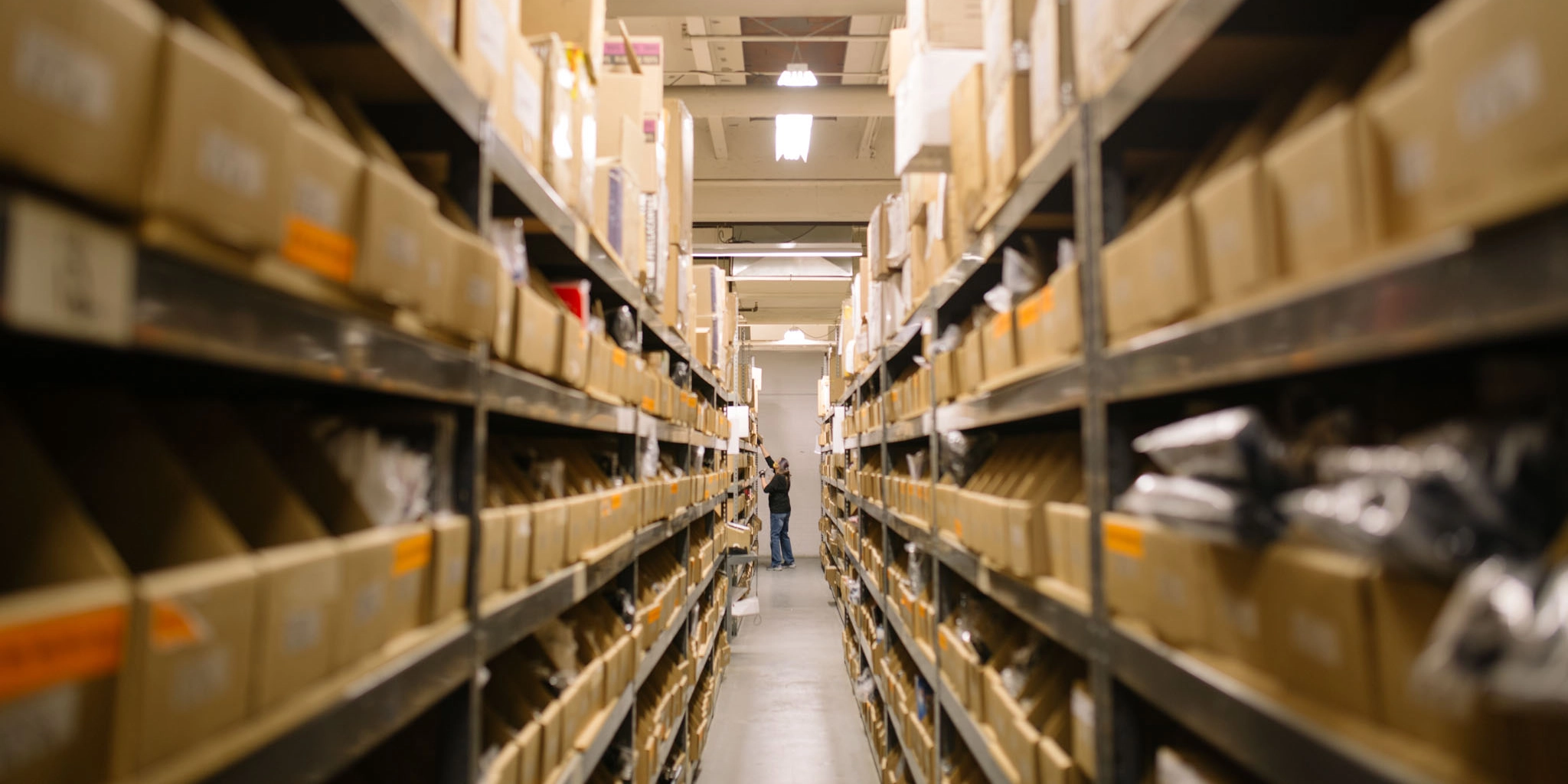
To paint a picture, imagine a customer in New York orders a book online. That order is routed to an Amazon fulfillment center in, say, New Jersey. Workers (or robots in some advanced warehouses) pick the book off a shelf, pack it, label it, and send it out via UPS or FedEx. In a matter of a day or two, the customer receives the book – voilà!
This quick turnaround is typical because fulfillment centers are optimized for speed and accuracy in handling direct-to-consumer (D2C) orders. They even process returns and restock items so that the inventory is always up-to-date.
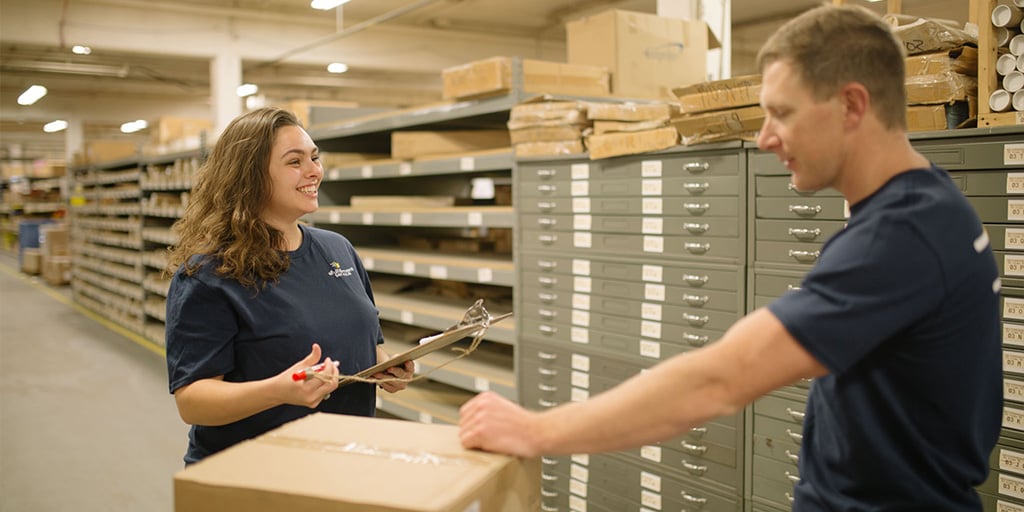
Fulfillment centers often operate as part of a third-party logistics (3PL) service or as the in-house logistics arm of large online retailers. For instance, Shopify offers its merchants access to a fulfillment network of warehouses to handle their orders.
The key point is that a fulfillment center is all about fast-moving inventory and direct customer satisfaction – getting goods out the door as efficiently as possible to keep those customers happy. You’ll typically find advanced software and automation here (think conveyor belts, barcode scanners, automated sorting systems) to manage thousands of small orders every day with precision.
Common tasks in a fulfillment center include:
- Storing inventory short-term: Products arrive from suppliers and are kept in organized bins or shelves until sold (usually not for too long, since high turnover is the name of the game).
- Picking and packing orders: When an online order comes in, staff or automated systems pick each item, pack it into boxes with appropriate padding, and label it for shipping. The process is often called “pick and pack,” and it’s a core function of fulfillment centers.
- Shipping to end customers: Fulfillment centers coordinate with parcel shipping carriers (like USPS, UPS, FedEx, DHL) to send out individual packages directly to end consumers. Fast shipping options (like 2-day delivery) are usually enabled by strategically locating fulfillment centers near customer hotspots, so distance and time to the customer are minimized.
- Handling returns and customer service logistics: If a customer sends something back, the fulfillment center can process that return, inspect the item, and return it to inventory if it’s in good condition. This keeps the cycle running smoothly.
Essentially, a fulfillment center is geared toward B2C operations, though they can handle B2B orders too when needed. They’re all about speed, efficiency, and accuracy for individual orders, ensuring that when you buy something online, it gets to you pronto. As one logistics company put it, a fulfillment center is “processing thousands of small orders per day, shipping each one to an individual address,” using specialized tech and processes suited for ecommerce.
What Is a Distribution Center?
A distribution center, on the other hand, is more like a waystation in the supply chain – a strategic hub where products are stored in bulk and then redistributed in larger shipments to other businesses or locations. If a fulfillment center is the sprinter handing off packages to delivery vans, a distribution center is the relay station handling the big pallets and crates, routing them towards retail stores or regional warehouses.
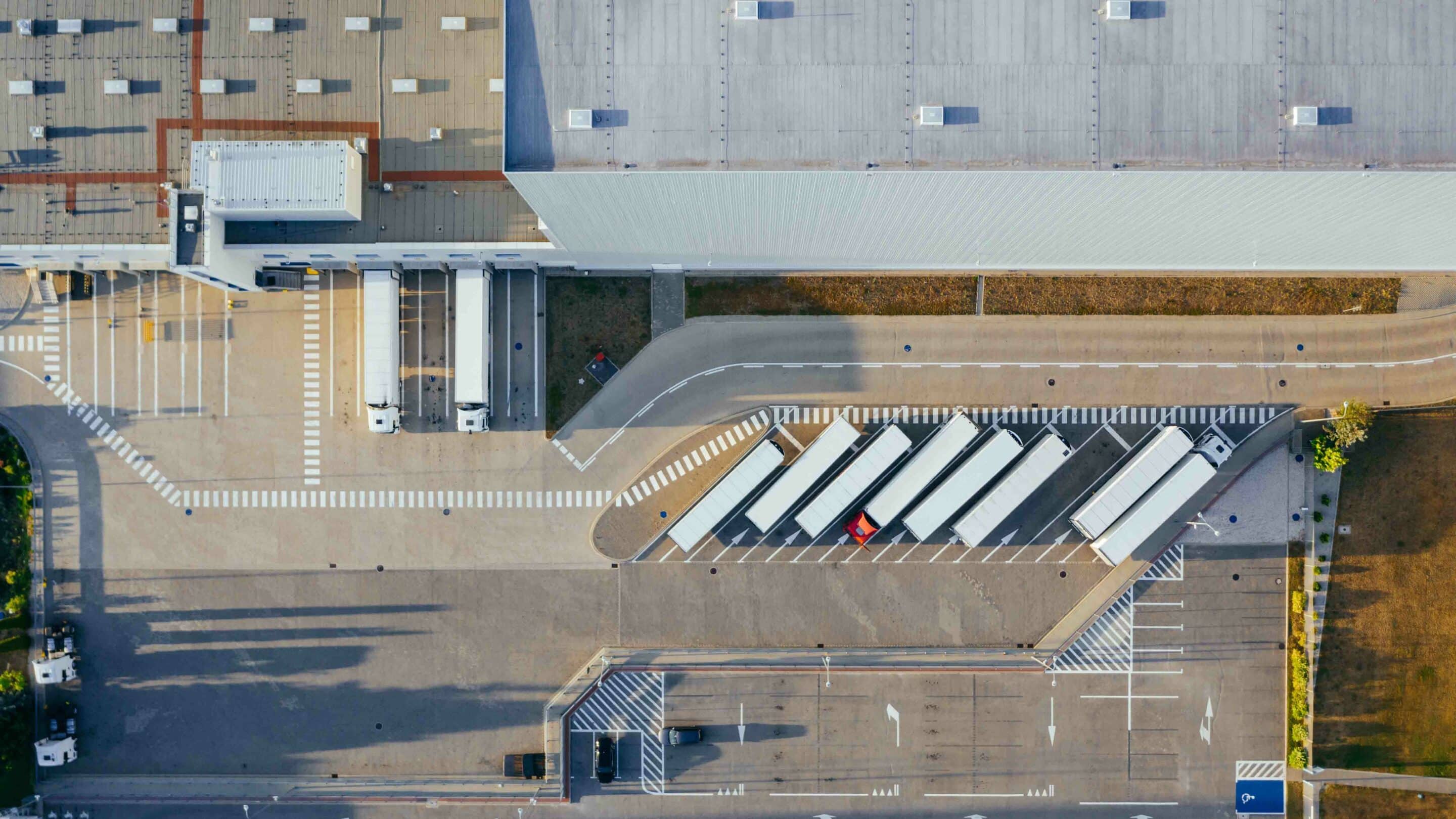
In simpler terms, a distribution center is a large warehouse that temporarily holds large quantities of goods on their journey from manufacturers to their next destination. These facilities are typically used by manufacturers, wholesalers, or retail chains as a midpoint: goods come in from production or suppliers, stay briefly, and go out to, say, various retail stores or sometimes to fulfillment centers that will handle the final leg. The primary purpose of a distribution center is to streamline the supply chain by positioning products closer to where there’s demand, thereby reducing overall shipping time and cost to those end destinations.
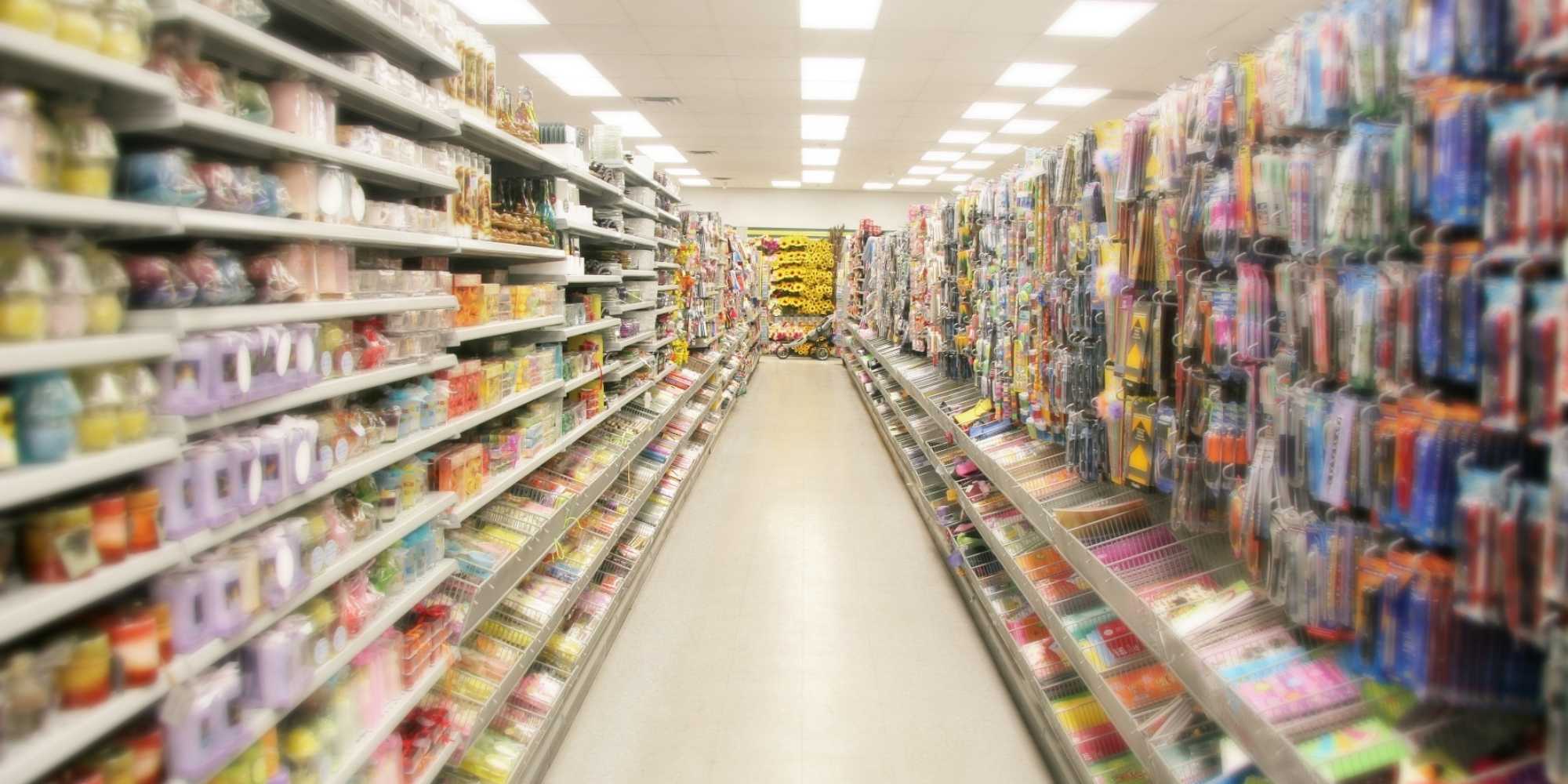
For example, consider how Walmart operates. Walmart doesn’t ship you a tube of toothpaste directly when you order one (they’re a retailer, not primarily an online seller like Amazon). Instead, Walmart uses massive distribution centers to supply their network of physical stores.
A supplier sends a bulk shipment of, say, popular toys or hundreds of TVs to a Walmart distribution center in a region. Those items are stored there until various Walmart stores in that region start running low on stock. Then the distribution center will load up trucks with pallets of merchandise and send them to each store to replenish the shelves.
Customers eventually buy the products in-store. The distribution center’s job was behind the scenes, making sure each store got the right products in the right amount at the right time. This bulk handling is all about efficiency and cost-effectiveness at scale – shipping goods in truckloads rather than piece by piece.
Key characteristics of distribution centers include:
- Bulk storage and redistribution: Distribution centers receive goods in bulk (often by the truckload or even railcar), and store them usually on pallets or in large lots. Products aren’t meant to sit for long; the idea is to keep them moving out to fulfill the needs of stores or other distribution points as demand arises. Think of it like a short-term holding and sorting facility for big shipments.
- Serving businesses, not individual consumers: Unlike fulfillment centers, distribution centers generally do not ship directly to end consumers. Their “customers” are retail stores, wholesalers, or sometimes other distribution or fulfillment centers. In supply chain lingo, distribution centers are typically handling B2B orders – business-to-business transfers of goods. They break down bulk shipments and send smaller batches out to multiple destinations (a process sometimes called “break bulk”).
- Hub-and-spoke model: Many distribution operations use a hub-and-spoke approach. The distribution center is the hub where large incoming shipments get sorted and sent out along different spokes (routes) to various endpoints. Shipping carriers like FedEx and UPS do this too: your package might travel to a regional distribution hub and then get routed onward. For companies, this means they might keep regional distribution centers so that stores in each region can be restocked quickly without every product having to ship from a far-away factory every time.
- Efficiency and cost focus: Distribution centers prioritize reducing lead times and shipping costs for large volumes of goods. They often coordinate multiple modes of transport – for example, a shipment might arrive by ocean freight or rail, then leave the center via trucks or even air cargo to reach its next stop. They also employ techniques like cross-docking, where incoming goods go straight to outgoing trucks without much storage, to speed up transfers.
Inside a distribution center, you’ll see equipment for heavy lifting and bulk handling: forklifts zooming around, pallet jacks, huge shelving racks for pallets, maybe even automation for sorting pallets. The tech systems in distribution centers are geared more toward inventory management and freight logistics (e.g., warehouse management systems for tracking pallets, and electronic data interchange systems to communicate with retailers’ inventory systems) rather than the fine-grained order picking tech you find in fulfillment operations.
Managing Fulfillment doesn’t have to be a hassle.
Partnering with a 3PL like eFulfillment Service means you can focus on growing your business while we handle the details. Request a Free Quote Today!
Fulfillment Center vs Distribution Center: Key Differences
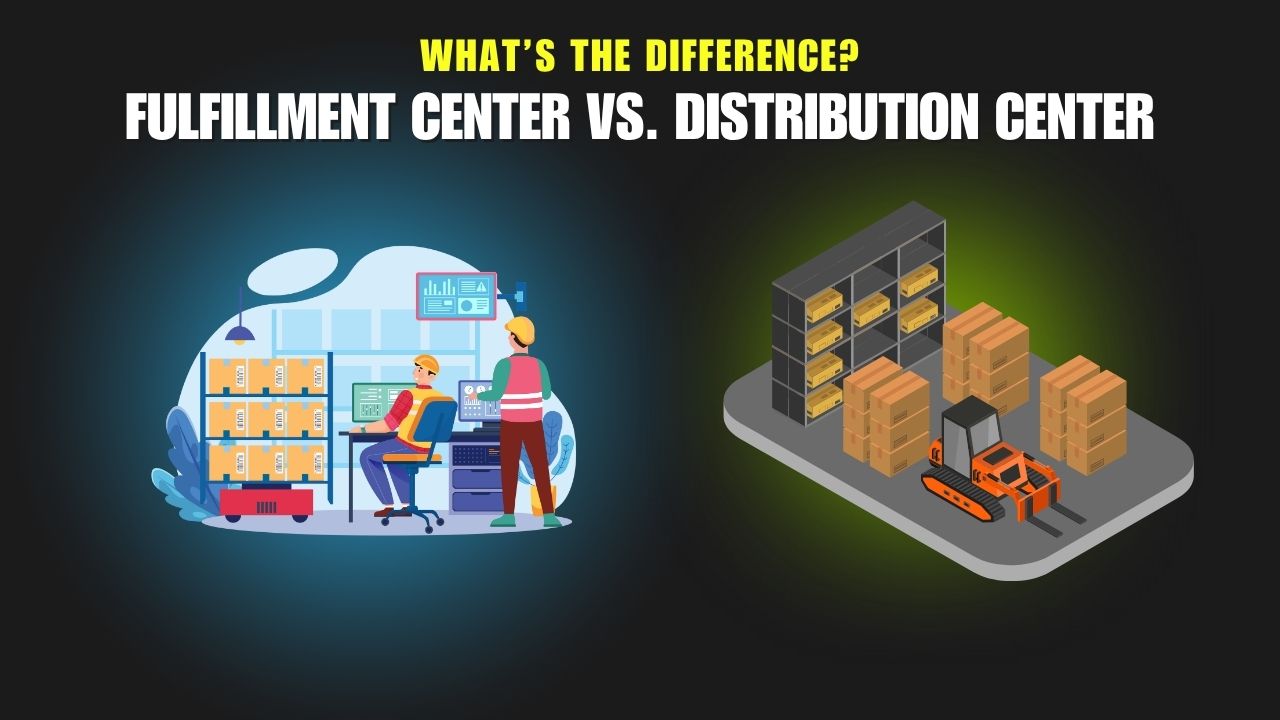
Fulfillment centers (left side) and distribution centers (right side) play distinct roles in the supply chain. Fulfillment centers specialize in processing individual orders and shipping directly to consumers’ doorsteps, while distribution centers handle bulk shipments, redistributing goods to retail stores or other business locations as a hub between manufacturers/suppliers and the final points of sale.
Now that we’ve defined each, let’s put them head to head. Are fulfillment centers and distribution centers the same thing? Nope – they might both be types of warehouses, but their day-to-day operations and goals differ quite a bit. Here’s a breakdown of the key differences in a nutshell:
End Customers (Who They Serve):
This is arguably the biggest difference. Fulfillment centers cater to end consumers, fulfilling orders for individual customers (think B2C – business to consumer).
Distribution centers cater to businesses, supplying product to retail stores, wholesalers, or even other warehouses (B2B – business to business).
For example, a fulfillment center might ship a single coffee maker directly to your home, whereas a distribution center might send a pallet of coffee makers to a chain of retail stores. If you ask, “Is a distribution center the same as a fulfillment center?” – the answer lies in who ends up receiving the goods: a customer vs. a store.
Order Size & Volume:
Fulfillment centers handle a high volume of small orders – thousands of individual packages flying out daily to different addresses. Each order might be just one or two items, and each is going to a different customer.
In contrast, distribution centers handle a lower volume of large orders – fewer shipments, but each shipment is big, often involving pallets or cases of product going to a single location.
You could say fulfillment centers are about many orders, small size, while distribution centers are about fewer orders, big size. One source neatly sums it up: a distribution center might move millions of units at a time in bulk shipments, whereas a fulfillment center processes countless individual units one-by-one for direct shipping.
Lower Your Shipping Costs with Smarter Fulfillment.
Partner with eFulfillment Service to move inventory faster and free up cash flow. We help Start-Ups optimize operations so products don’t sit on shelves. Request a Free Quote today!
Purpose & Role in Supply Chain:
Fulfillment centers are the final step in the supply chain before the product reaches the customer’s hands. Their purpose is to quickly turn around orders – store just enough product to fill current orders and upcoming short-term demand, and keep it flowing out.
Distribution centers are an intermediate step, a bridge between production and the retail environment. They redistribute inventory across a region or network, ensuring stores or local fulfillment nodes have what they need. Put simply, “a fulfillment center fulfills customer orders directly, while a distribution center helps move bulk inventory through the supply chain”.

Storage Duration & Inventory Turnover:
Because of their roles, fulfillment centers typically hold products for a short time – the goods are in constant motion, arriving and leaving quickly (high turnover) to meet customer orders. It’s not about long-term storage, it’s about being a revolving door of inventory.
Distribution centers also strive for fast turnover, but they might hold onto stock just a bit longer than a fulfillment center would, as they wait for the right timing to ship to stores. They don’t keep products for years (that would be more like traditional warehousing), but the storage is temporary until allocation is needed elsewhere.
In other words, warehouses (in the classic sense) are for long-term storage, whereas both fulfillment and distribution centers are about moving products through rather than letting them sit – with fulfillment being ultra fast-moving and distribution being fast-moving at a pallet scale.
Operations & Technology:
Order fulfillment vs. freight management – that’s a big operational difference.
In a fulfillment center, you’ll find pick-and-pack operations, individual item tracking, and systems designed for ecommerce logistics (inventory systems giving real-time stock levels, integrations with online stores, etc.). Workers (or automation) pick items from bins, and there’s a focus on things like optimizing the picking routes, packing stations, and labeling for last-mile delivery.
In a distribution center, the operation is more about bulk handling and coordination: you see pallets being moved, orders that might be “ship 500 units of X to Store #123,” and tech that focuses on managing large shipments (like freight routing software, barcode systems for pallets, and scheduling trucks).
For example, a fulfillment center might have conveyor belts and sorting robots for small packages, while a distribution center has loading docks lined with 18-wheelers and maybe cross-docking areas where goods go from inbound to outbound quickly.
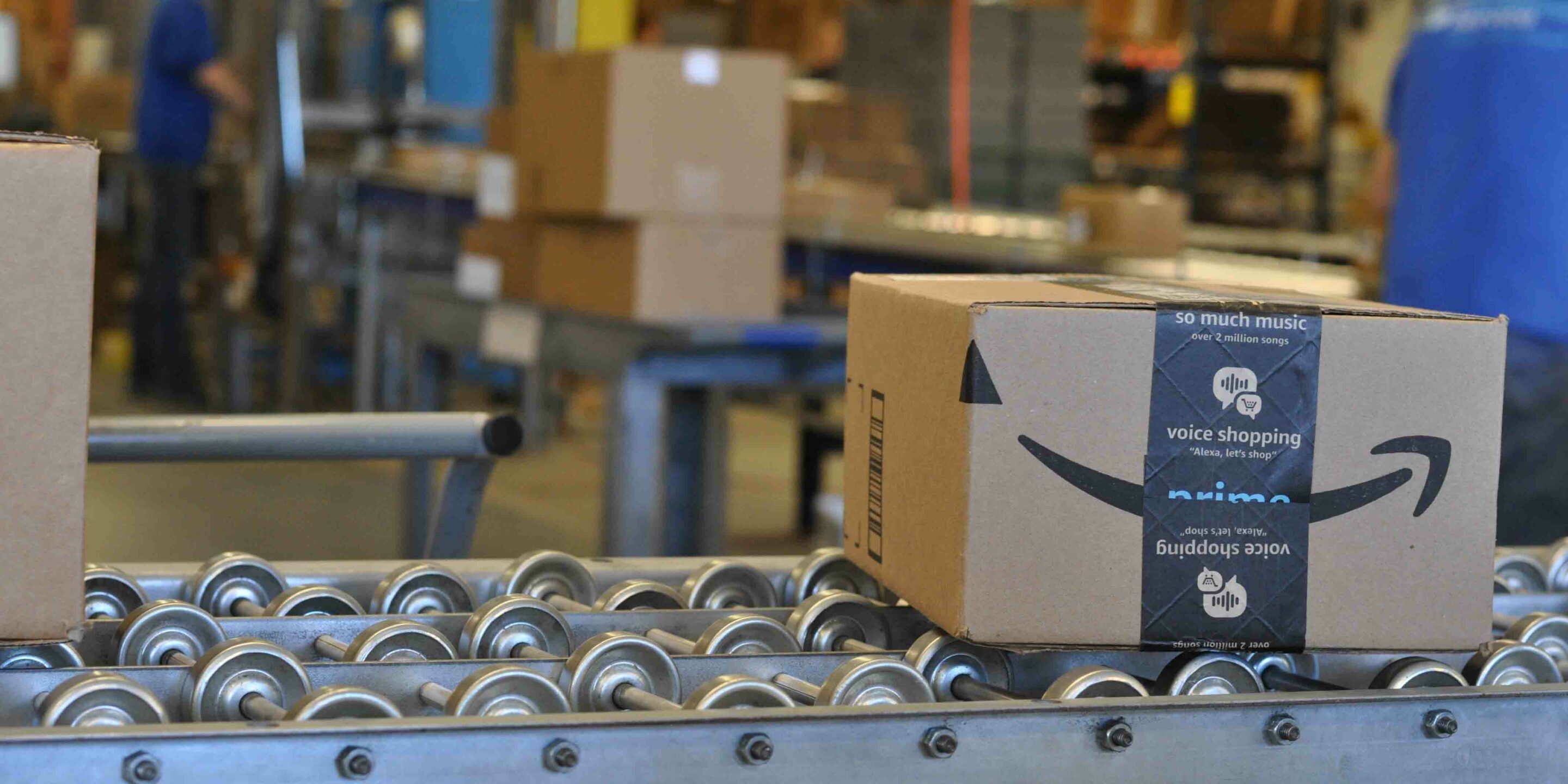
Examples in Practice:
To crystallize it, consider two giants: Amazon vs. Walmart.
Amazon, the king of e-commerce, operates via a vast network of fulfillment centers – huge warehouses where each item is picked for individual customer orders and sent straight to the shopper. When you order that book or gadget from Amazon, it likely ships from one of these fulfillment centers.
Walmart, a retail giant, relies heavily on distribution centers – massive hubs that take in products from suppliers and distribute them out to all the Walmart stores in the region. If a toy is manufactured overseas, it might go to a Walmart distribution center in the U.S., then be trucked to hundreds of Walmart store locations, where customers will eventually buy it in person.
Amazon does have some distribution centers too (especially for distributing inventory across its network), and Walmart has been expanding e-commerce fulfillment, but traditionally this Amazon-vs-Walmart contrast highlights the difference well.
Which Does Your Business Need? (Choosing Fulfillment vs Distribution)
By now you might be thinking, “Alright, I get the difference – but which one do I need for my business?” The answer comes down to your business model, sales channels, and scale.
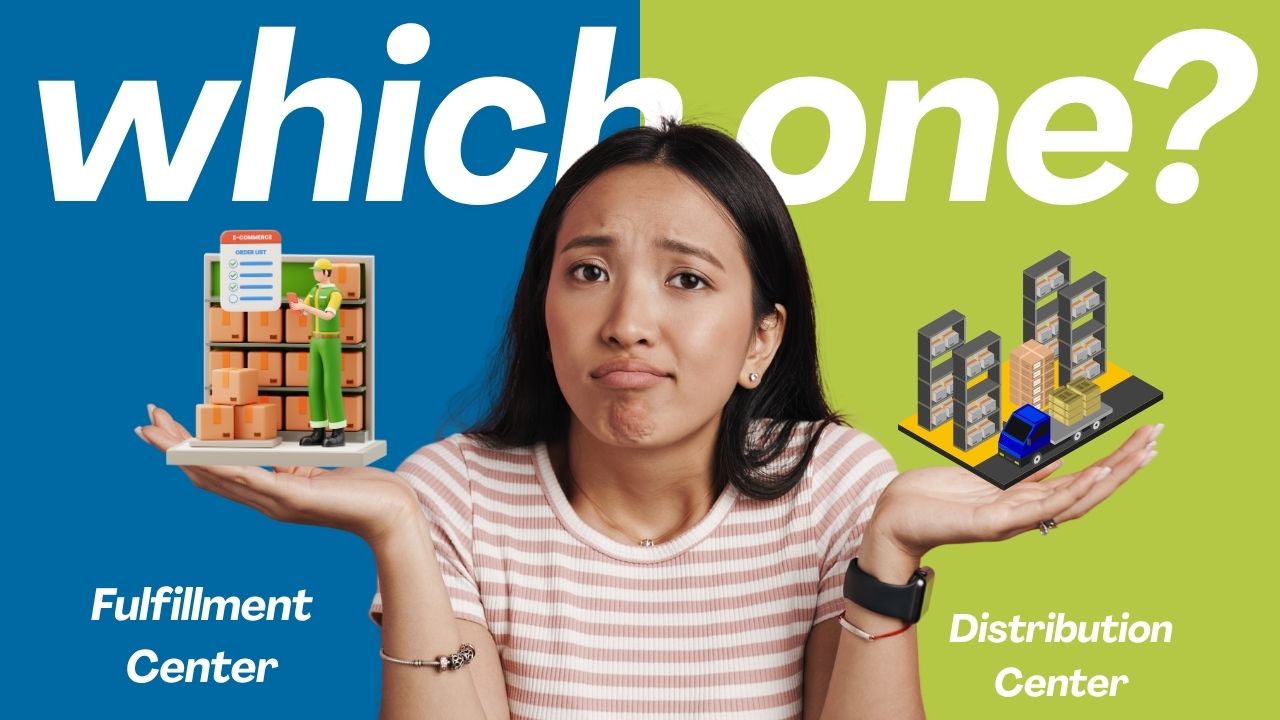
If your business sells directly to consumers (D2C)
For example, you run an online store, ship subscription boxes, or have a Kickstarter product that you’re sending out – a fulfillment center is likely your best bet. Fulfillment centers are built to handle the complexities of e-commerce logistics. They’ll take care of storing your products, packing each customer’s order, shipping it out quickly, and even handling returns and customer service elements.
For many small and medium e-commerce businesses, partnering with a 3PL fulfillment center (or using services like Amazon FBA, Shopify Fulfillment, etc.) makes a ton of sense. It saves you from the headache of running your own warehouse and lets you offer fast, professional shipping to your customers from day one.
As a bonus, many fulfillment partners can scale up during your busy seasons – you know, those holiday rush times – so you don’t have to worry about outgrowing your garage or small warehouse space. Speed, flexibility, and customer satisfaction are the big wins here.
On the other hand, if your business is focused on selling in bulk or through other businesses (B2B)
Say you’re a manufacturer supplying retailers, or you distribute products to a network of stores – then a distribution center might be the cornerstone of your logistics. Distribution centers shine when it comes to efficiency at scale.
They allow you to consolidate inventory in strategic locations and then redistribute it cost-effectively. If you have, for instance, ten retail storefronts across the country, you might use a regional distribution center to stock all your products and then truck them to your stores as needed. This ensures each store gets restocked promptly without each store needing massive storage space on-site.
High-volume businesses love distribution centers because shipping out pallets of goods in one go is cheaper (per unit) and easier to manage than sending hundreds of individual packages separately. You get centralized control over inventory and can optimize transportation – for example, shipping full truckloads is cheaper than many partial loads.
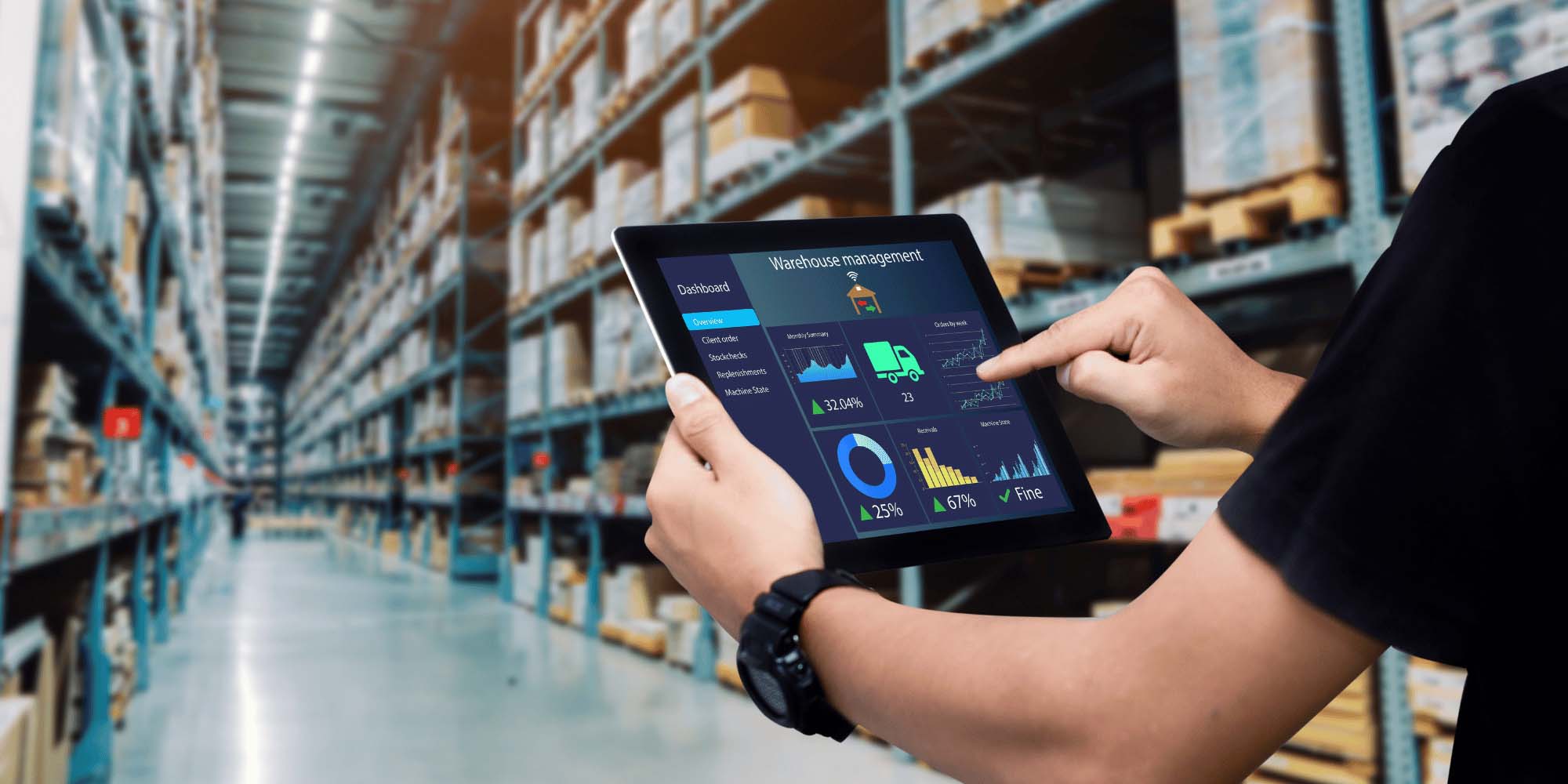
Could it be both?
Absolutely. Many larger companies use both distribution centers and fulfillment centers in tandem to cover all channels. For instance, a big omnichannel retailer might keep overflow stock or slow-moving products at a distribution center, send inventory to stores from there, and also feed their online order fulfillment from there.
Then they might have a separate fulfillment center (or several) that specifically handles the direct online orders. In fact, some advanced operations have hybrid centers or use 3PL services to manage this seamlessly. Using both isn’t overkill if you have both B2B and B2C components – it can actually save costs and improve delivery times by letting each part of the logistics puzzle do what it’s best at.
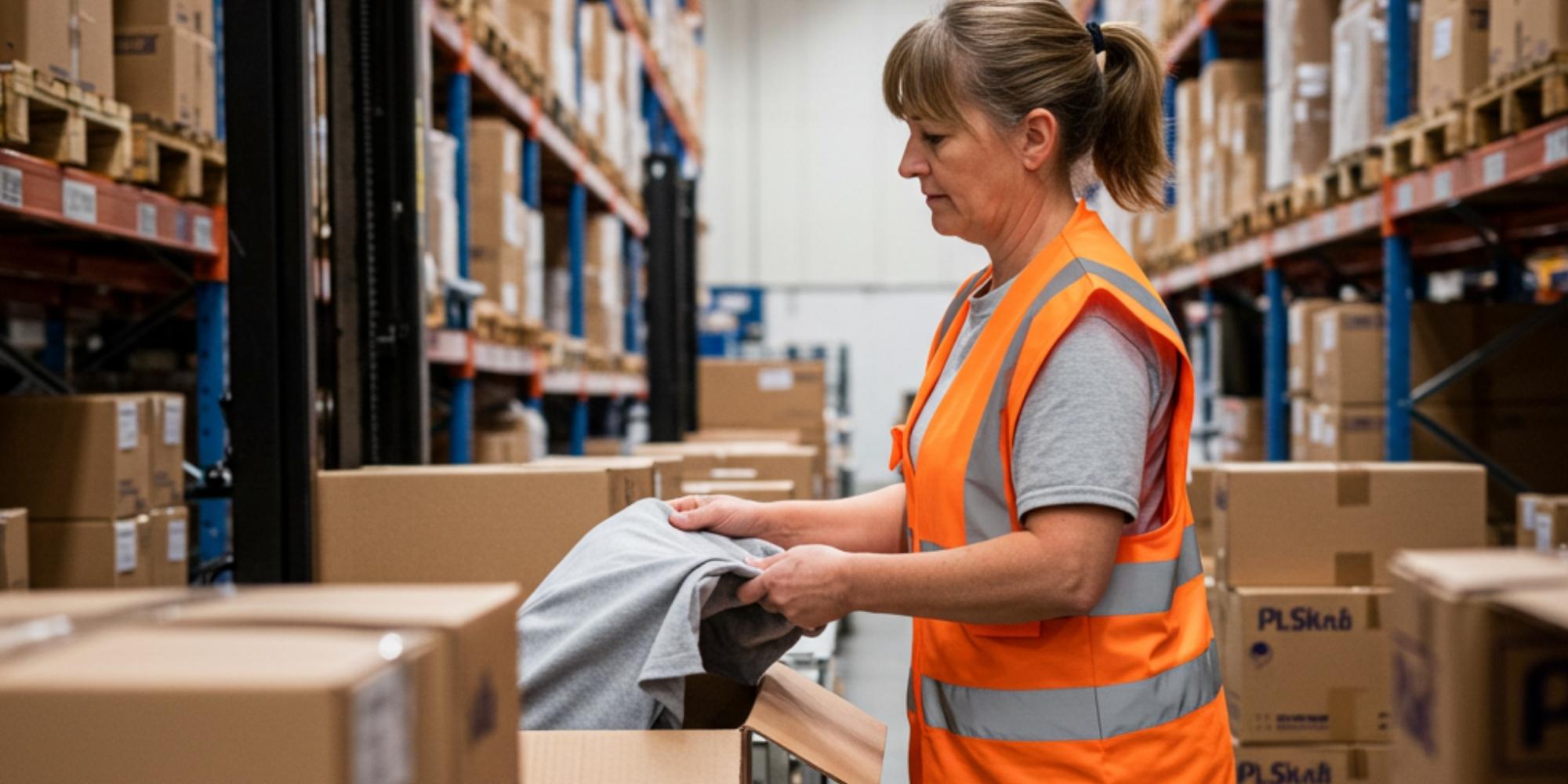
For example, a large ecommerce business might store its bulk inventory in a central distribution center (cheaper storage for large volume) and then as online orders come in, that stock is sent to regional fulfillment centers that can pack & ship to customers quickly.
Many large ecommerce businesses use both: they “store large volumes of products in distribution centers and use fulfillment centers to process and ship individual orders”. The bottom line is, you don’t necessarily have to choose one exclusively – you choose what combination fits your needs.
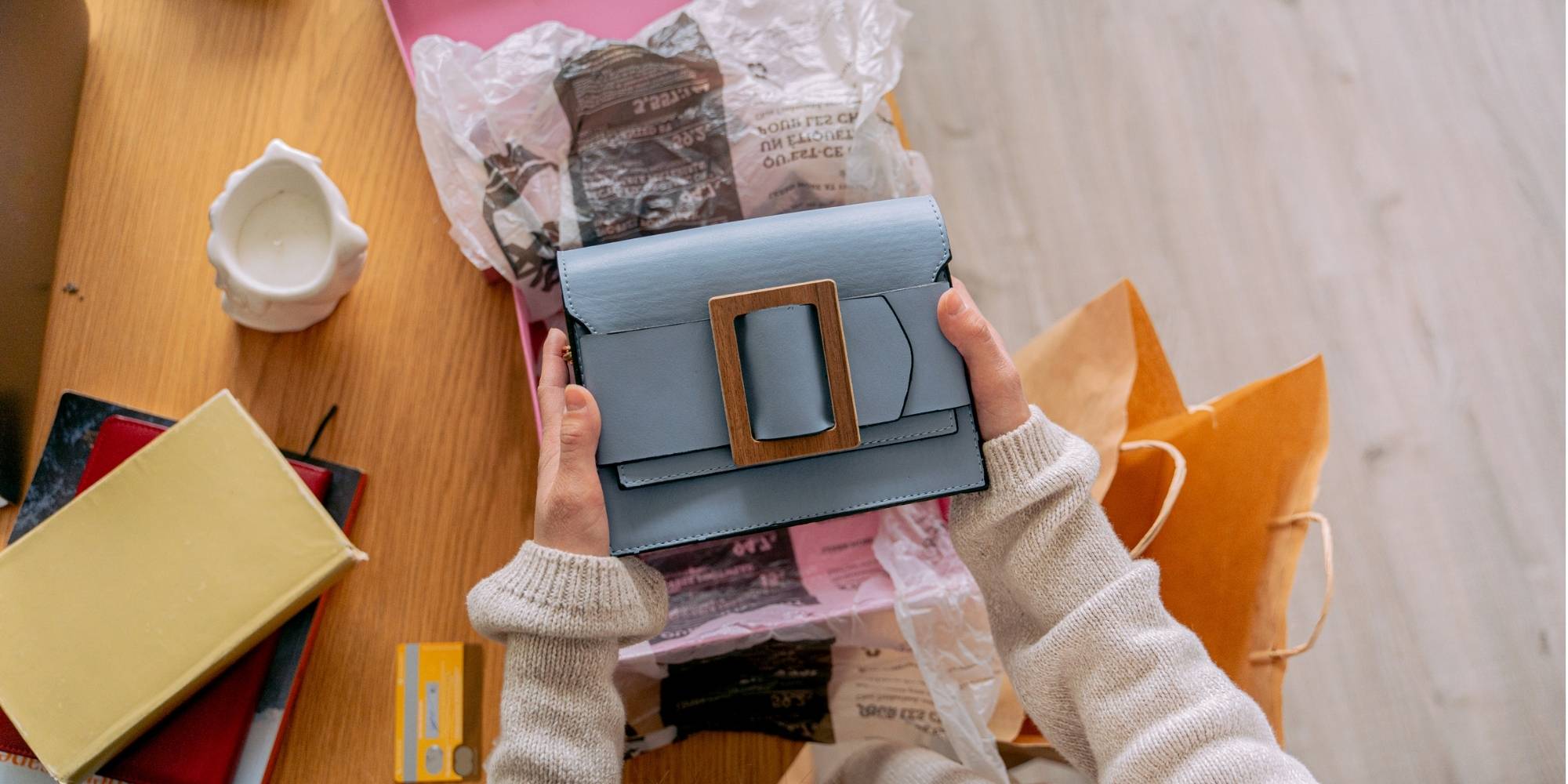
Consider your priorities:
If fast delivery to customers and handling lots of small orders is your world, lean toward fulfillment services. If managing a supply network and optimizing bulk deliveries is key, focus on distribution capabilities.
It’s all about the right tool for the job. And if your business grows, don’t be surprised if you find yourself needing to re-evaluate and possibly incorporate both models to cover new channels (for instance, many brands that started online-only have later set up distribution centers when they began selling wholesale or in retail stores).
Also, think about cost-effectiveness. For a small e-commerce operation, renting a huge warehouse to use as a distribution center would likely be overkill (and costly). Using a fulfillment center or 3PL where you pay for just the space and services you use might be more cost-effective.
Conversely, a big company shipping to hundreds of stores might find it more economical to run a distribution center than to ship store orders out of a fulfillment center that’s geared towards small packages. It really “depends on your business model” and volume.
Take a hard look at where your shipments are going: to individuals or to business locations, in what quantities, and how fast they need to get there. That will usually point you in the right direction.
FAQs: Fulfillment Center Vs. Distribution Center
Is a distribution center the same as a fulfillment center?
No – they’re related but not the same. A fulfillment center is a specific type of warehouse focused on fulfilling online/customer orders, while a distribution center is focused on shipping goods in bulk to other business locations. The main difference lies in their end customers: fulfillment centers serve end consumers, whereas distribution centers serve retail outlets or wholesalers. So, if a facility is sending out individual packages to Jane Doe and John Smith, it’s acting as a fulfillment center. If it’s sending out pallets to Big Retail Store #12 or to another warehouse, it’s acting as a distribution center.
What is the main difference in how a fulfillment center and distribution center operate?
The core operational difference is in order size and processing. A distribution center might receive a million phone chargers from a factory and then ship out 100,000 units each to ten different electronics stores – big, bulk orders to a few destinations. A fulfillment center might receive those phone chargers and then ship out one charger to each of a million individual customers who bought them online – small orders to many destinations. Fulfillment centers excel at pick-pack-ship for each order, while distribution centers excel at large-scale sorting and routing of goods to the right place in the supply chain.
Can one facility serve as both a fulfillment center and a distribution center?
In some cases, yes. The lines can blur, especially as businesses adopt technologies and try to be efficient. You might find a big “smart warehouse” that handles both functions under one roof – for example, it might ship out bulk orders to stores and also handle online orders for the region.
Some fulfillment centers (particularly those run by 3PLs or large retailers) do have sections or processes for wholesale orders, effectively doing distribution work in addition to D2C fulfillment. That said, typically the two are kept separate or have separate workflows even if in the same building, because the infrastructure and processes for each can be quite different.
Many large companies simply operate distinct facilities for each to avoid confusion and optimize each process. So while it’s possible (and some advanced operations do it), most businesses will designate a facility primarily as one or the other.
Is a fulfillment center basically a warehouse?
Yes, a fulfillment center is a type of warehouse, but with a specialized purpose.
Unlike a traditional warehouse that might just store goods long-term, a fulfillment center is a hands-on, active warehouse that is constantly receiving products and then picking, packing, and shipping them out to customers. If a warehouse is like a storage pantry, a fulfillment center is like a busy kitchen – ingredients (products) come in and quickly get turned into finished dishes (packed orders) going out to diners (customers). The building might look like a warehouse, but it’s operated very dynamically with a focus on throughput rather than storage.
Which is more cost-effective for my business – using a fulfillment center or a distribution center?
It really depends on your business needs and scale.
For small or mid-sized ecommerce businesses selling directly to consumers, using a fulfillment center (especially through a 3PL) can be more cost-effective because you pay for only what you use and you benefit from their optimized shipping rates and infrastructure.
You don’t have to invest in large warehouse space or hire a big logistics team – the fulfillment provider handles it, letting you focus on growing your business. On the flip side, for a larger operation that ships in bulk (like a manufacturer or a brand with many retail partners), having a distribution center can save costs by enabling bulk shipping and central inventory control.
There’s no one-size-fits-all answer; it’s about matching the solution to your sales model. Often, businesses do a cost analysis: if the majority of orders are individual online sales, fulfillment centers usually win on cost and efficiency; if the majority is bulk orders to stores, a distribution setup might be more efficient.
Can an ecommerce business use both types of centers effectively?
Yes, and many do.
As mentioned earlier, large ecommerce players often use a hybrid approach: they might keep their main stock in distribution centers (cheaper to store large volumes in a few central spots), and then allocate inventory to various fulfillment centers closer to customers or use those fulfillment centers to handle the actual packing and shipping of individual orders.
This way they get the best of both worlds – cost efficiency in bulk handling and speed in last-mile delivery. If you’re a growing ecommerce business, you might start with one model and add the other as you expand channels. For example, you could start D2C with a fulfillment partner, and later if you start selling wholesale to retail stores, you introduce a distribution center for that side of the business.
Using both isn’t redundant if each is serving a different channel or purpose. It’s all about scaling smartly and ensuring your supply chain is optimized for both consumer orders and retail distribution when needed.
Summary & Key Takeaways:
In the grand scheme of things, both fulfillment centers and distribution centers are heroes in the logistics world – each with their own superpowers. Fulfillment centers shine in getting products to individual customers quickly and efficiently, keeping that online shopping experience smooth and satisfying. Distribution centers excel in the behind-the-scenes work of keeping businesses supplied, making sure stores and regions never run out of the products people want. They might occupy similar-looking buildings and share some logistical DNA, but now you know that when it comes to fulfillment center vs distribution center, the differences are not only real – they’re critical for choosing the right strategy for your business.
So, next time you click “order now” or stock your store’s shelves, you’ll appreciate the journey your product took – and you’ll be savvy enough to decide whether a fulfillment center, a distribution center, or maybe a bit of both, is what keeps your business moving and your customers happy. After all, getting the right product to the right place at the right time is what logistics is all about, and understanding these concepts is a big step toward running a lean, mean, supply chain machine. Happy shipping!
Sources:
- Shopify Blog – “Fulfillment Center vs. Distribution Center: Essential Differences (2025)”
- NextSmartShip – “Fulfillment Center vs. Distribution Center: Key Differences” (2023)
- WSI (Warehouse Specialists) – “Distribution vs. Warehousing vs. Fulfillment”
- eFulfillment Service – “Fulfillment Center vs. Distribution Center: Which is Best for You?”
Ready to talk shipping solutions? The team at eFulfillment Service is happy to help answer questions and set you up for fulfillment success. Here’s to fewer headaches and more growth ahead!
0 Comments